Constructing Textiles: Emma Cogné
The TLmag Award winner at Tremplin 2018 is Emma Cogné with her project Système T. We caught up with her to find out more about her pipe and rope textiles
Yellow pipes, green pipes, long pipes, flexible pipes. Every kind of pipe fascinates the young designer Emma Cogné who recently won the TLmag Award for her project Système T – a series of textile structures made from construction pipes and ropes. The award was chosen from a group of graduates who exhibited in Tremplin at the WCC•BF gallery, Brussels. Graduating from the Master’s course in Textile Design, at La Cambre (ensav), Brussels, earlier this year, Cogné challenges the notion of what a textile is as well as it’s lifecycle by departing from the use of traditional materials of yarn and thread.
Lise Coirier, TLmag’s editor-in-chief, says: “Emma Cogné wonders about the interior and exterior space and her textile creations meet both functional and aesthetic uses. Her textile designs, made of knots and rope assemblages, seem elementary but lead to a quite sophisticated formal rendering and very colorful visual impression. They filter the light to create a beautiful contemporary shade or divider. Textile design here takes on a spatial dimension that gives rise to multiple formal combinations and personal appropriations.”
We caught up with Emma Cogné to dig a little deeper into the world of pipes, ropes and textile design:
TLmag: How would you describe your design practice?
Emma Cogné: In my work, I investigate and question the materials of my immediate environment. Using man-made materials in textiles I am constantly reminded of their humbleness and enjoy finding alternative ways to use them in the fields of architecture and interior design.
Why did you decide to use construction materials for your project?
When I came to Brussels, I was surprised at the number of building sites which have invaded the city. I started to collect plastic pipes with no real idea of what I could make with them, I just saw beauty in them. I wanted to work with only a few elements and make visible a material which usually hidden inside walls. Throughout the project, I progressively discovered the aesthetic and technical potential of this material. It is low cost, recyclable, weather-resistant and easy to transport. By experimenting with it, I found surprising outcomes that could be translated into a functional textile wall.
What were the challenges of doing a textile project with man-made materials?
The challenge was to produce textile objects from a material which is not designed for this use. I had to find solutions in the manufacturing processes, building upon its qualities and maximize its best possible use. I developed an elementary craft technique through knotting systems to create assemblies. The Plastic pipes can be broken down and put back together like a construction set. The rope connects the system. It is used for its resistance, elasticity, to make “a whole” from separate elements. Each material remains intact. Nothing is definitely fixed and the textile surfaces can be unlaced and then reused. In response to the ecologic crisis and material flow, this project called for an economical use of resources. My aim was to produce a resistant textile object which can also be recycled. I have focused on transforming plastic pipes into a textile wall to show both the possibilities and the issues associated with the use of man-made materials in today’s architecture.
Can you tell us about the final pipes you used in your project?
A pleasant surprise along the project’s journey was when I contacted a company which specializes in the manufacturing of pipe, the Polieco Group. I wanted to find a reliable resource. I explained my project with drawings and samples, and they agreed to help me. I received more than 1000 meters of pipes in various sizes and colors. Thanks to their support, I could produce on a larger scale, creating customized products to conform to the architecture.
Cover image:
Système T, Turbo Gliss, 2018
ICTA Sheath, polypropylene rope
190 x 70 x 2,2 cm
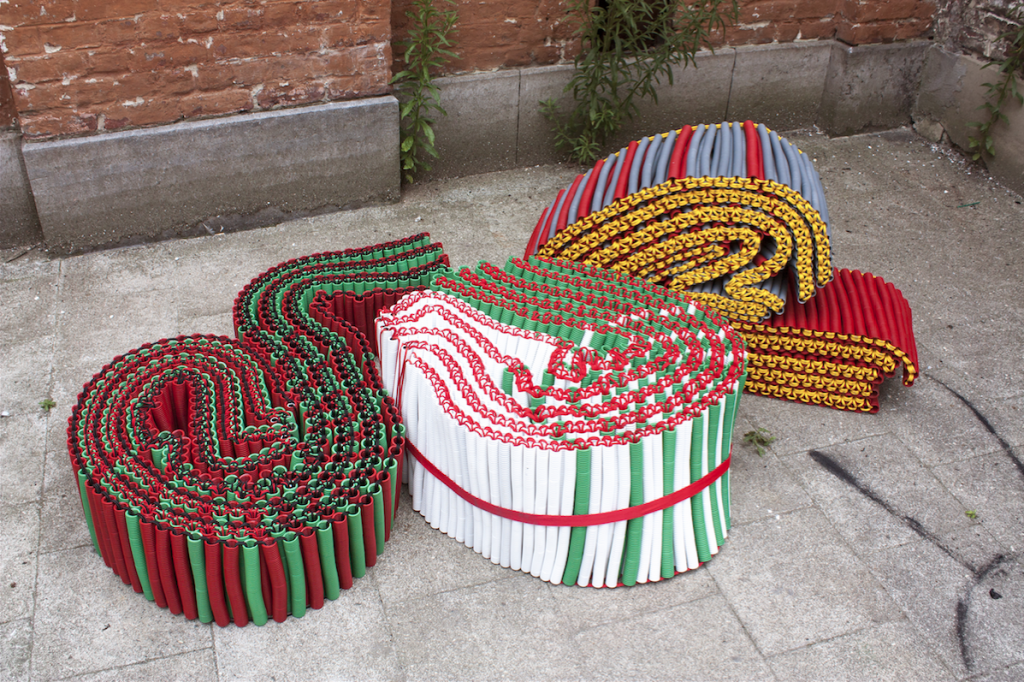
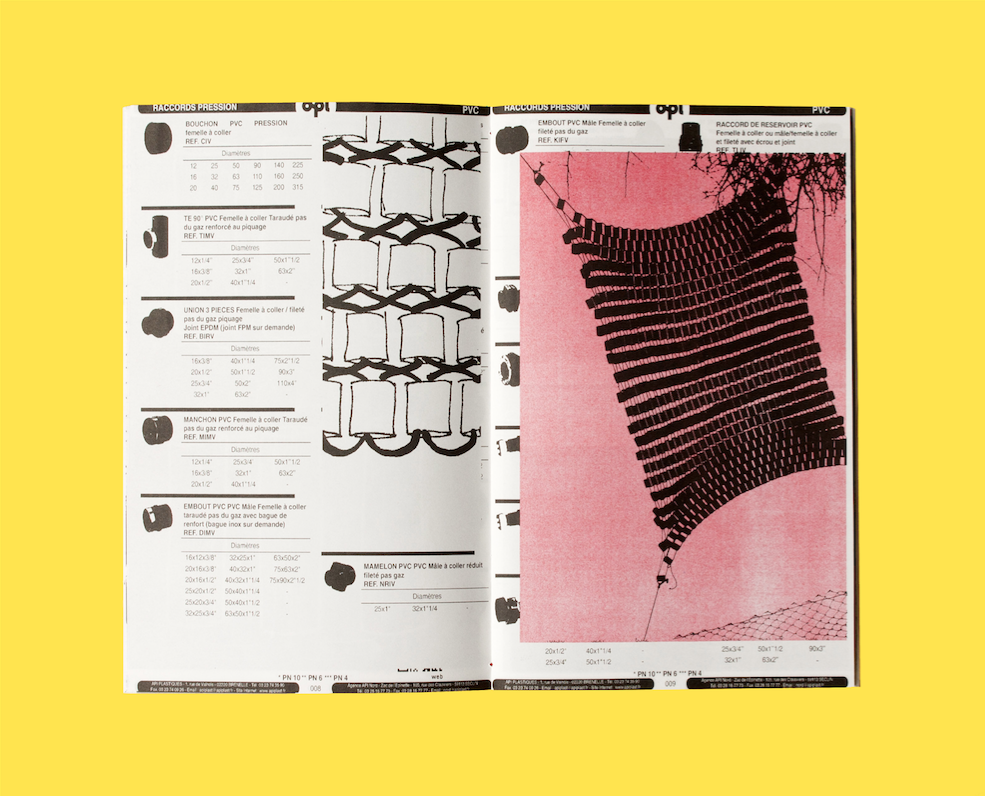
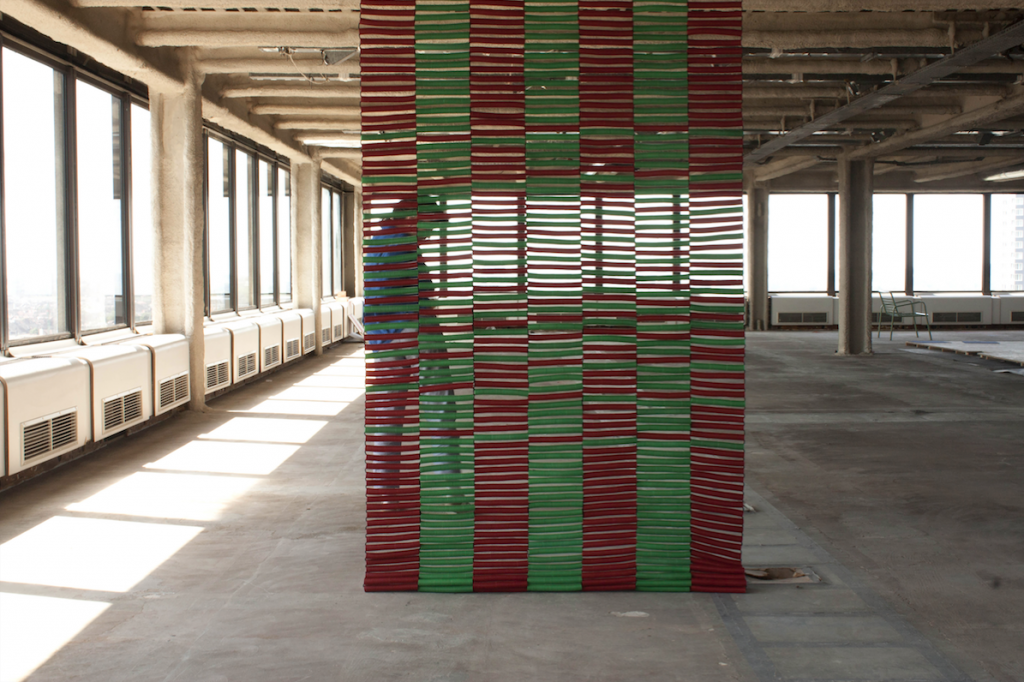
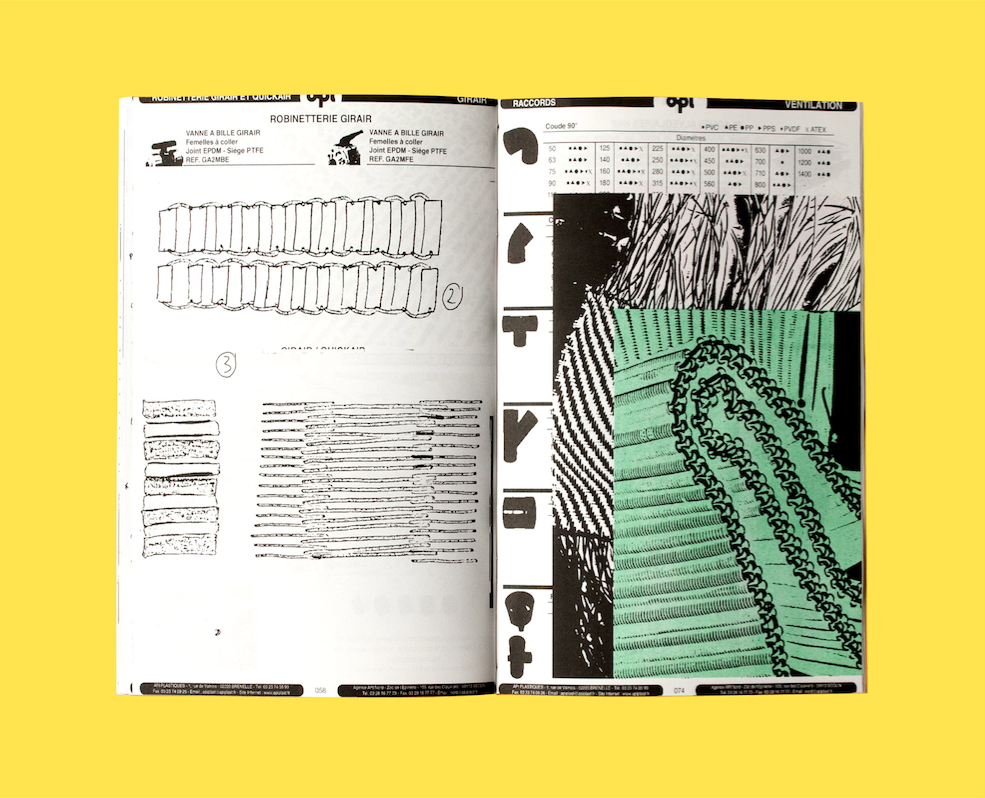
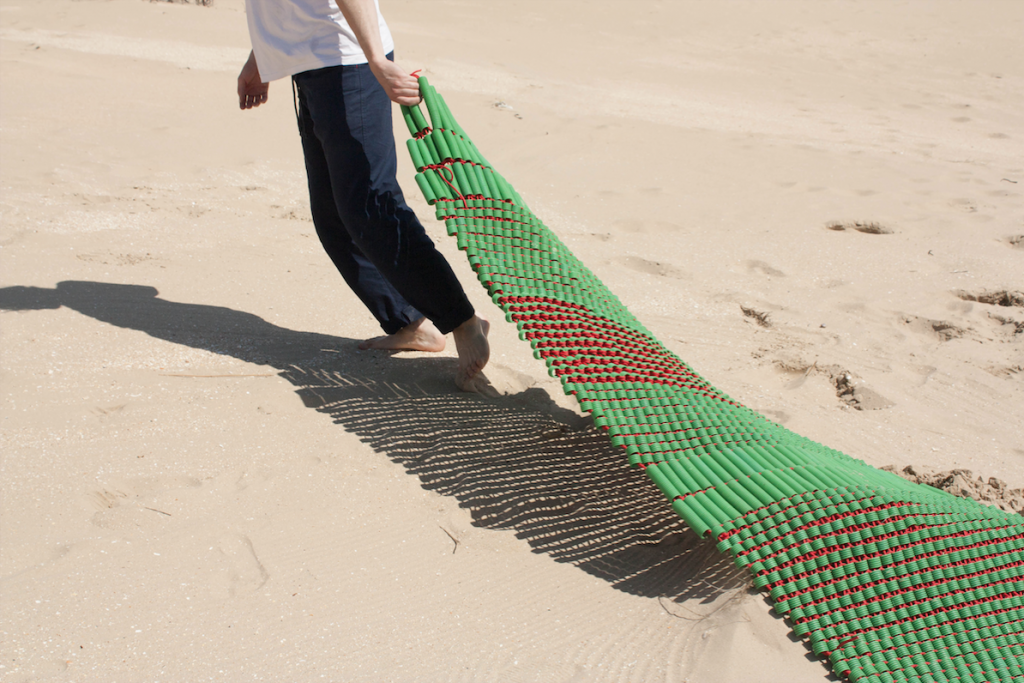