Charlotte Kidger: Waste Forager and Materials Designer
TLmag talks to Material based designer Chalotte Kidger about her ‘Industrial Craft’ collection which is made from the waste streams of CNC manufacturing
Although Charlotte Kidger only just finished her MA in Material Futures at Central Saint Martins earlier this year her project Industrial Craft that repurposes polyurethane waste from CNC manufacturing has been the subject of much attention. TLmag catches up with Kidger in her London based studio to discuss the project and what she has lined up for London Design Festival (LDF) 2018:
TLmag: Maybe you could start by telling us a bit about your background and how this lead you to work with waste materials?
Charlotte Kidger: I started off doing my Bachelors degree in a course called Printed Textiles and Surface Design at Leeds College of Arts and I was always super interested in more than just flat surfaces. I was always fascinated by how I could manipulate the surface of a material and pushing the limits with what was possible. I have always been process driven. For example, I’d use machines that were ideally for wood but instead put plastic on them. I was always testing and experimenting. I had this curiosity behind materiality.
And then, someone suggested doing the MA in Material Futures so I looked into it. I had never really considered 3D sculptural materials or hard materials prior to that.
I spent the first year researching, doing loads of different projects and then for the final year I just knew that I wanted to do something that was very hands-on, very process driven and given everything that is going on with plastics, decided to go down that avenue. And
then, even still at that point, I wasn’t sure where it would lead me because the research was through the making. I’ve kept experimenting with different composites and what I could mix it with, how I could use it and then I ended up with this quite durable and hard material. Then the question became how can I transition that into 3D objects? Then the vessels and the tables came from that.
Did it take a very long time to find the right combination of composites?
Yeah, there were some points where I was thinking ‘this just isn’t going to work’. I was creating quite an interesting palette of materials but nothing that would be durable enough to use in a larger volume. Obviously, because there is so much of this plastic that goes to waste I wanted to be able to do something that was going to be able to use it in a larger volume and going to last. I tested different glues, dissolving it, breaking the composition down through heat, making it into a solution but none of these would be feasible on a big scale. So then I started looking into resins and that really worked and I thought ‘ah, okay! We’re getting somewhere’. Although I had to keep pushing that, there was still a lot more testing with that to get the ratio and the set time right, and adding the pigments… so a lot of experimentation. It is really fun when something comes out and it looks good and you get a result that you weren’t expecting.
So you add the pigments to get the bright colors?
The polyurethane foam dust is actually a yellow color. It is polyurethane foam and it comes in a grey, pink, orange, yellow and white but the company I worked with mostly use the yellow color. So then I add a pigment during the casting process. I add the pigment to the resin and then add the plastic into it and that completely colors it. I wanted it to be that as much is one during the casting process as possible so that when I take it out of the molds there was not any finishing or anything that needs to be done to it.
You mentioned earlier “all the stuff that is going on with plastic at the moment” was there a particular story or something that led you into the specific CNC plastic?
Obviously, it’s a very niche plastic, it’s not your standard domestic plastic. I started off looking at household plastics but there’s just so much happening with it – obviously with Precious Plastics by Dave Hakkens leading the foreground for what was happening there and I wanted to do something a bit different. I started looking into industrial waste streams so I went off the plastic a bit and started industrial foraging – going around different industrial estates and speaking to people about what waste streams they had coming out of their processes and I came across Bakers Patterns, a CNC company based in Telford. I went to visit them and they had a really large volume of this plastic dust, almost a skip a week so they were super super keen for me to start working with them. They thought it was amazing that a designer had approached them and wanted to work with their waste stream.
At that point I wasn’t aware of the waste that comes from CNC and the research led me to visit them and when I realized how big it was I thought ‘wow. this is just one company’. There are numerous companies around the world and quite a few in the UK alone so it became an immediate challenge. How can we harvest this as a new raw material?
The company was great. They are so supportive and want to help me in whatever way possible. I am going to work with them in the next few weeks on some new moulds and other ideas that focus more on the circularity of my whole process.
Do you think they have a bit go a guilty conscience over the amount of plastic they are putting into the world?
I spoke to them a lot about their opinions on that. Like you say, you would think that they would want to keep quiet about it. They always try to recycle and want to recycle but there is not any infrastructure for them to be able to. There’s nothing there to help them. The company that takes their waste away creates energy from waste through incineration. But they are a particularly good removal company because they try to have 100% of material diverted from landfill whereas I know that a lot of companies aren’t like that. The project opened them up to thinking about it more.
Is there no alternative material they could use?
I asked them whether they could see this material not being used anytime soon and if there will always be a demand for it. They said yes because in the design industry people make their prototypes from this foam before they make their final pieces. That is always going to happen. No matter how good digital renders are, people need to see the physical, the tangible to scale. They also do a lot of work for the film industry. They were speaking about CGI and even though it is amazing it is not as good as the real thing so all these massive budget films will still be using this. They can’t see it dying out anytime soon.
I’ve had a few people comment and say “you shouldn’t be encouraging the use of this foam” but it is there you can’t deny the fact that it is still being used. There is a demand for it and while there is a demand for it – and the same for all plastics and waste materials – we should try to use it as a new raw material. My project is touching on certain elements of the problems but if we work collectively we can push more of a change. You can’t tackle the whole problem of plastic alone. You need people working on different parts of it.
One of the important things with my pieces is that I am encapsulating the plastic within something that is durable and is going to last so it’s hopefully creating something that’s maybe an heirloom and has longevity.
Is the resin bio-resin?
It is not a bio-resin. I did do some research and testing with bio-resin but it wasn’t getting the same results and then there is the question of if it is bio-resin and that then decomposes then the plastics will then leach out. So at the moment, it doesn’t make sense to use it. I am definitely interested in looking into other possibilities. I am applying for some funding at the moment to do research with some bio-resin companies because there is still so much research that needs to be done.
Can you tell us a bit about the Material of the Year show at LDF?
The whole idea that Jimmy MacDonald is proposing revolves around the name of the show ‘Beyond the Chipper’. So it is about showcasing designers who are doing more than grinding up plastic and looking at different ways of using plastic as a raw material.
What else do you have lined up for LDF?
I also have some work with Colour of Saying by Laura Perryman for ‘Colour Via’ held at Surface Matter. The exhibition looks at disruptive use of colour and how color will change the more we use waste material. I think it’s a really good concept and it relates to something I want to do over the summer where I’d like to visit all the different CNC places and collect the waste material from all their different colored plastics. I want to do a few pieces based on just the natural colors without any pigment. That’s kind of my next little project. I’ve got some new vessels that will be showing at
Mint Shop. I’ll have some samples and other pieces with different window displays and installations around Brompton Design District and Shoreditch Design Triangle also.
So it’s has a lot of interest then…
Yeah! I am very overwhelmed by it. I wasn’t expecting at all. It’s been really nice having the positive feedback. I always wanted to have my own studio when I finished my MA but if you don’t have the demand it’s hard to motivate yourself and find the drive to do it as you don’t know if people will be interested or if people want it.
What was the inspiration behind the shapes of the pieces?
The title of the project ‘Industrial Craft’ came from the fact that I was always on industrial estates doing the research. So the inspiration was very industrial based – the corrugated surfaces, the pipes, industrial buildings, modernist shapes.
Also, because of the casting technique and the material I have to design the forms in a way that works with the material. Some of the molds were actually made from pipes that I found within the industrial estate and others from sheets of corrugated material that I found
and then I use silicone, jesmonite and fibreglass to make the molds.
Material of the Year: Plastic Beyond the Chipper will be on display at the Old Truman Brewery from September 20–23
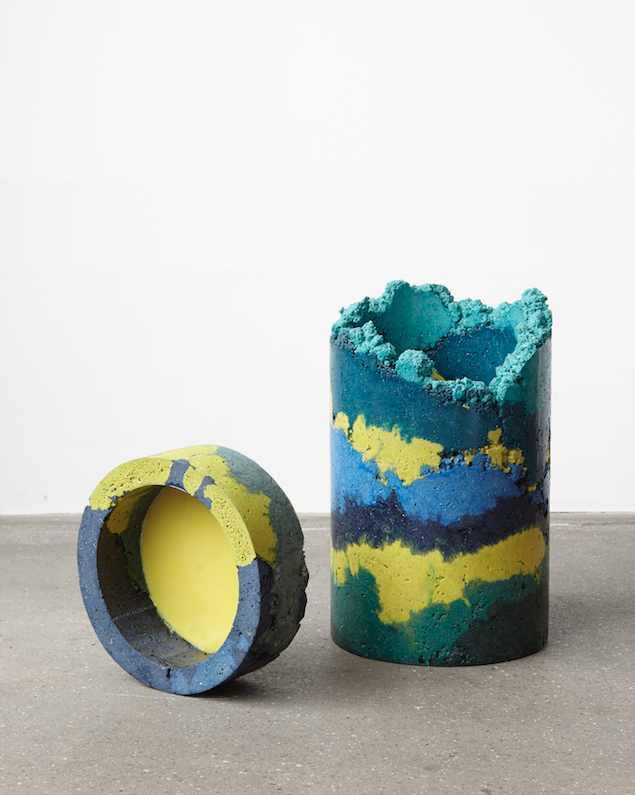

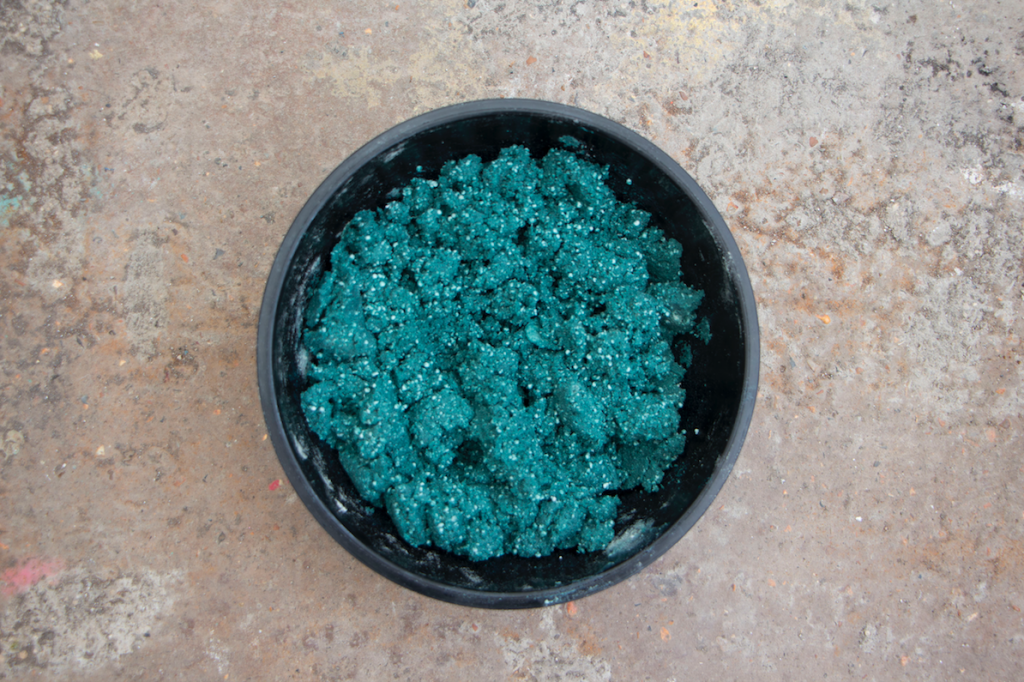
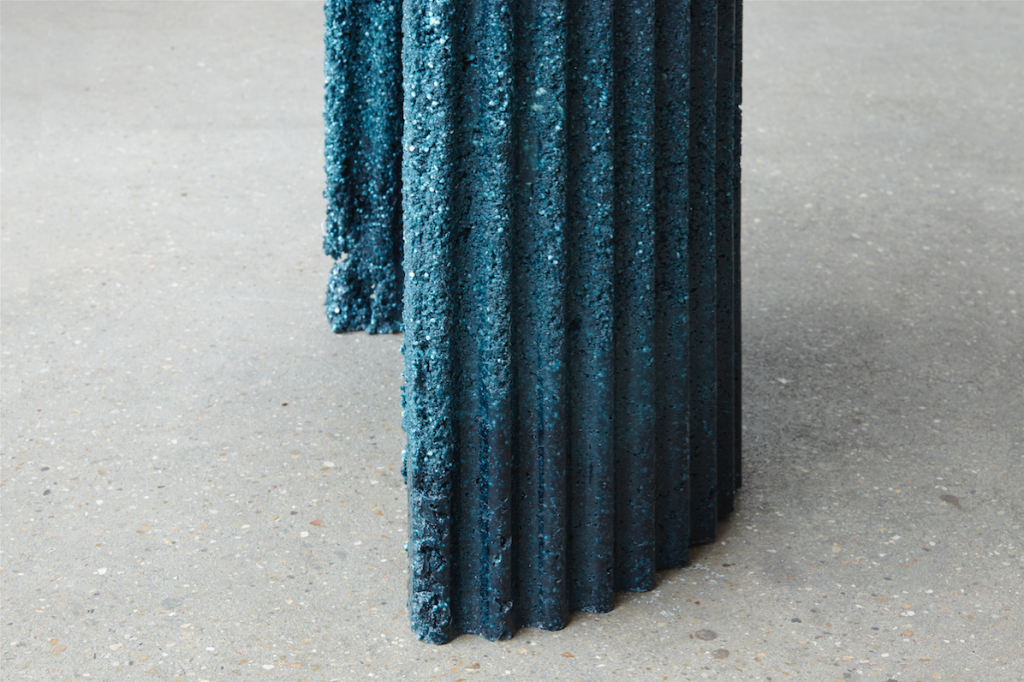
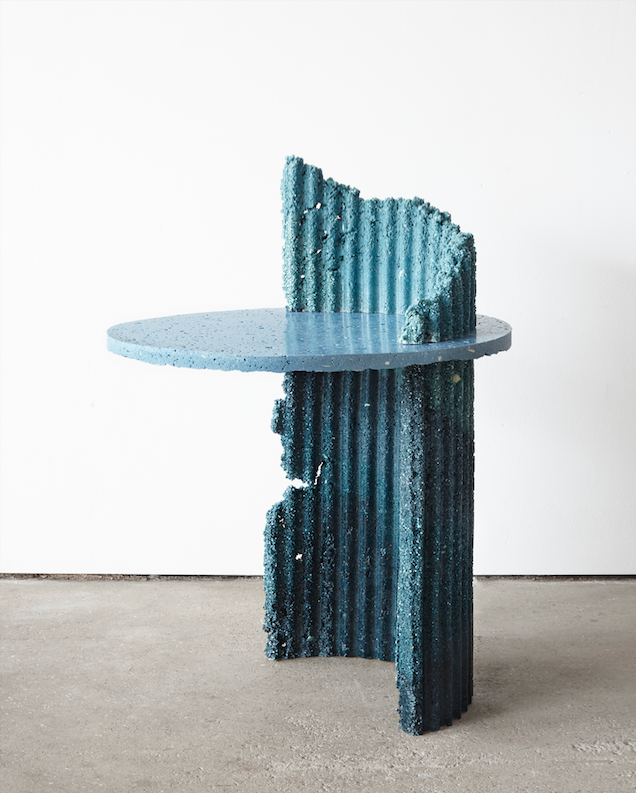