Mendel Heit: Weather or Not
Currently showing at Musée du Cristal Saint-Louis, Maison&Objet and Spazio Nobile, designer Mendel Heit spoke to TLmag about how he works in the new age of post-craft.
Form, durability and craft are the three things Mendel Heit believes we value the most in design objects. Based in Berlin, the French-German designer works closely with craftsmen and digital manufacturing techniques to uncover new design applications. Commissioned by the FRAC Lorraine and Hermès Foundation, his new XXL Cumulus installation is included in the Over The Rainbow exhibition at the Musée du Cristal Saint-Louis. He also launched new work for Vista Alegre at Maison&Objet and is included in Spazio Nobile’s Silver Edition exhibition until February 19. Heit spoke to TLmag about how he works in the new age of post-craft.
In what ways does your use of digital manufacturing become craft-like in, for instance, your porcelain work for Vista Alegre?
To me, traditional crafts and digital manufacturing rather have to benefit from each other. They can be used individually or combined in various ways. One being the prototype state of the other, or being mixed in the fabrication process. Craftsmanship is an endless source of human experiences, and well-honed knowledge of materials and techniques. Many times, it has a very long tradition, and many working processes are already very efficient. On the other end, digital manufacturing enables designers and manufacturers to explore variations and prototype efficiently. It also allows an exponential, not yet fully explored, complexity in shapes and functions. I don’t think that digital manufacturing should take on crafts, I believe there is more of mutual benefit to find in that relationship, and also depends on the type of product you design.
In the development of ceramic and porcelain designs I made recently, like Midnight for Vista Alegre, digital manufacturing techniques helped me a lot to explore models of design variations, that would have taken a lot of time and resources by hand otherwise. I explored surface texturing and relief decorations with digital tools to simulate quickly and take design decisions. But the final manufacturing techniques used are done by gifted craftsmen and -women with very few digital manufacturing. In this case, the digital has a more discreet position.
On the other hand, for the 3d printed eye-wear I made for Framepunk, digital manufacturing is the main actor. The 3d printing process uses its full potential here, because we produce custom-fitted eyeglasses. We all have very differently physiognomies, and one-size eyewear does not provide the best experience and correction, but 3D printing can. Then the colouring and surface finish is made by hand. In this case, digital manufacturing makes a lot of sense as the main production technique. It enables individual configuration and simplifies the production.
Besides products and furniture for brands, you have worked extensively with Maker Labs too. How has this influenced your methodology and aesthetics?
My activity in Makerlabs and Fablabs has been to learn, share and explore the possibilities of making. First of all, it was about meeting people, engage dialogues for example about intellectual property, 3d printing or even traditional crafts. It was a gathering of like-minded people but also surprisingly different backgrounds. This allowed me experiment in very different fields like programming open source electronics, upcycling old objects into new tools, try desktop manufacturing, laser cutting, CNC milling, and even learn a bit about weaving and screen-printing. It felt like an extension of my studies, with ties to the real world. To make these experimental place work, we also had to figure out ways to sustain the project.
In terms of design and shape language, I was able to start an exploration on generative shapes, and yet complex structures. These led me to making 3d printed jewellery pieces, with shapes that would be very difficult to achieve with normal methods, like the ones I later made for Stilnest. Later, this inspired me for the generative vase Tombola, where each ceramic or glass piece made is different from the previous. In terms of methodology, I deepened my taste for exploration, but also gave me the chance to learn about thinking and idea organisation techniques. This experience also led me more precise definitions about the most suitable solution: does it make sense to 3d print this, or can we just make a quick cardboard model?
This Makerlab format is still open, and continues to be valuable experiences for designers and makers, but also for people with new business ideas. You might learn to position yourself in the middle of crafts, digital manufacturing and socially relevant matters related to it. On one hand you can learn to build your own 3d printer, but also how to make a device to break the TV signal when you want more family time. For me it was eye opening on how much people value crafts, the human experience behind objects and manufacturing technologies. It was a time for networking and experimenting, and constructive human interaction! We organised many outdoors events in different cities with the aim to meet people and get them to participate in making and exploring with us. People care about how and by whom it’s made. I am certain that design studios and many other departments already profit a lot from creative contexts offered in Fablabs and maker spaces.
For Cumulus, the form is inspired by a childhood memory. How important is form still in relation to new manufacturing methods and materials?
To me, an object communicates in many ways. At first, you see the image of a miniature cloud, that grabs your attention. Then a closer, more tactile analysis tells you about the quality of the glass it’s made of, strong and yet fragile. But then, how was this shape blown into glass? Who made it? This is where the craftsmen and -women become part of the value of the object.
New manufacturing techniques can enhance greatly the complexity of form, offer a new depth of texture variations and at the same time, the engineering, lightness and strength can also be optimised to its peak. There is definitely a new freedom for designers’ imagination in that area. You can do anything that your 3d software enables you to produce. It will certainly bring new challenges in the culture of shapes and in the definition of what makes sense. But still, finding the right process, within the given context (durable efficiency, resource availability, human well-being) remains a central pillar, which digital manufacturing should continue to nourish. Sometimes the solution is fully 3d printed, sometimes semi-industrial, traditionally crafted, or even a mixed model of manufacturing methods.
Finally, the way an object is made is as important as what it means to its owner, and how well it functions: the form you see that triggers your emotions and your memories, the durable quality of that kitchen tool that never let you down, and the story of the gifted people who manufactured it are important. I think these are three things that we value in objects.
Season III – Silver Edition, design & Silvano Magnone, handmade photography, Spazio Nobile, Brussels (BE), 24.11.2016-19.2.2017, www.spazionobile.com
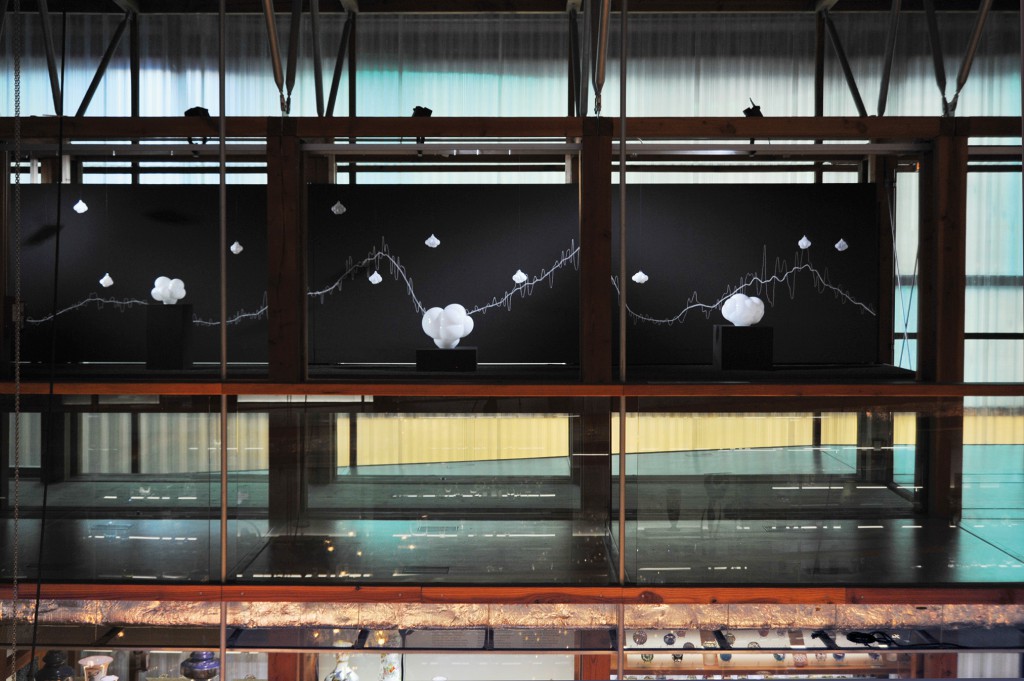
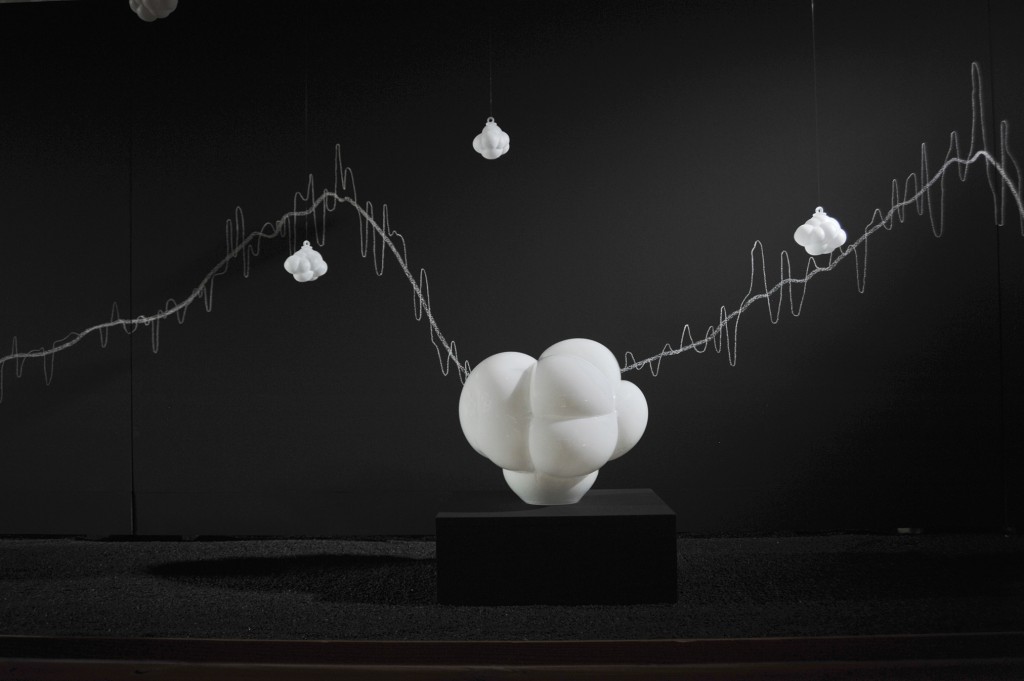
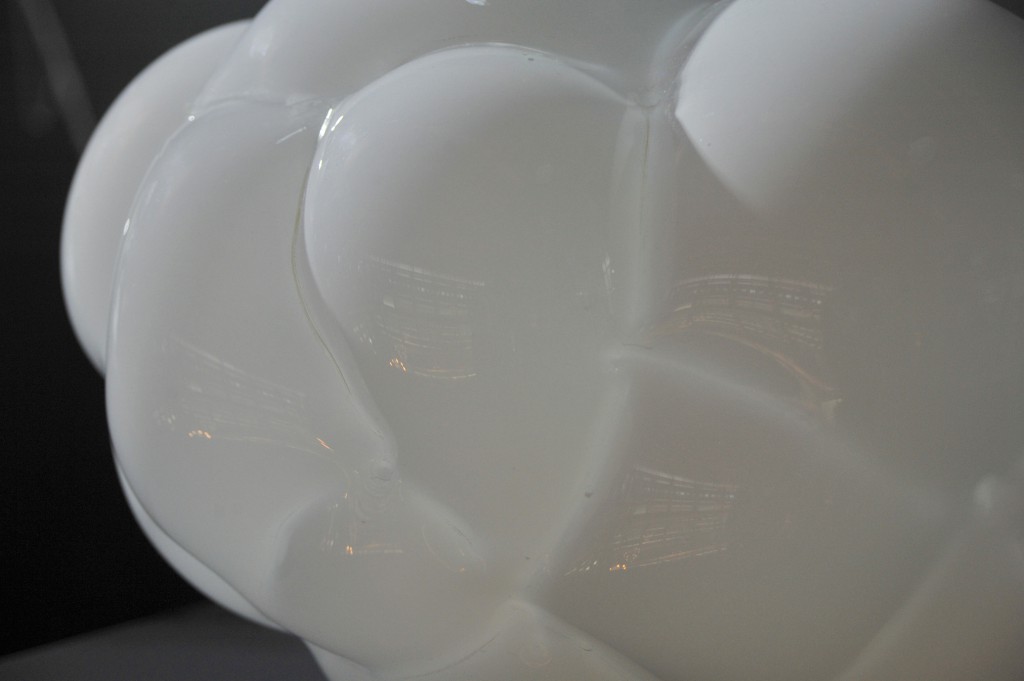

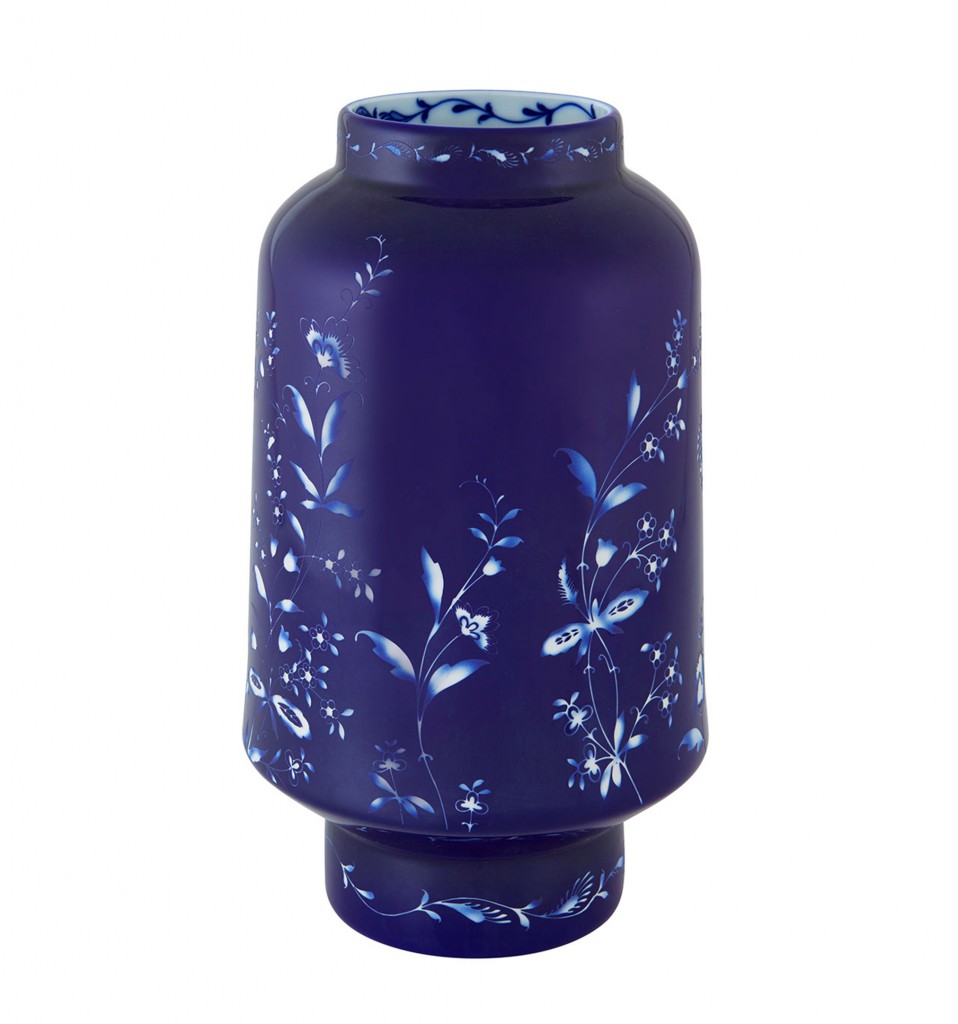
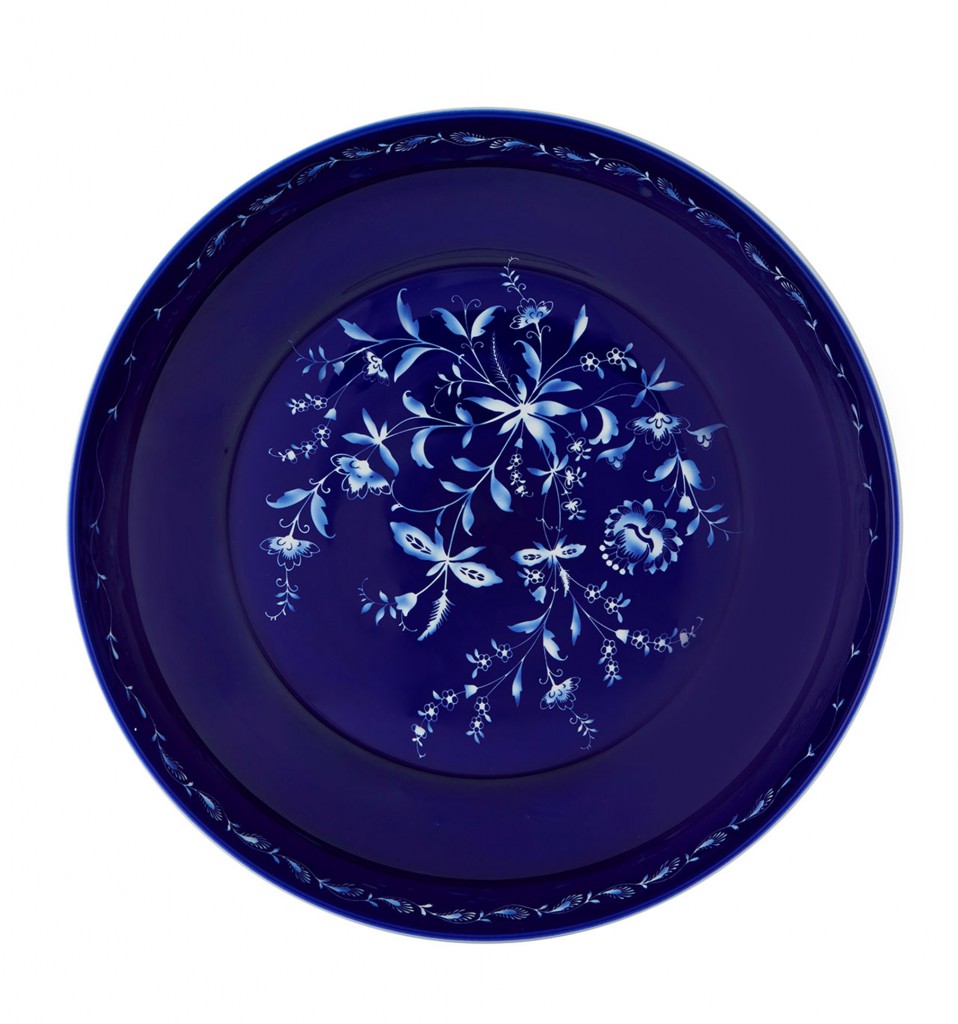
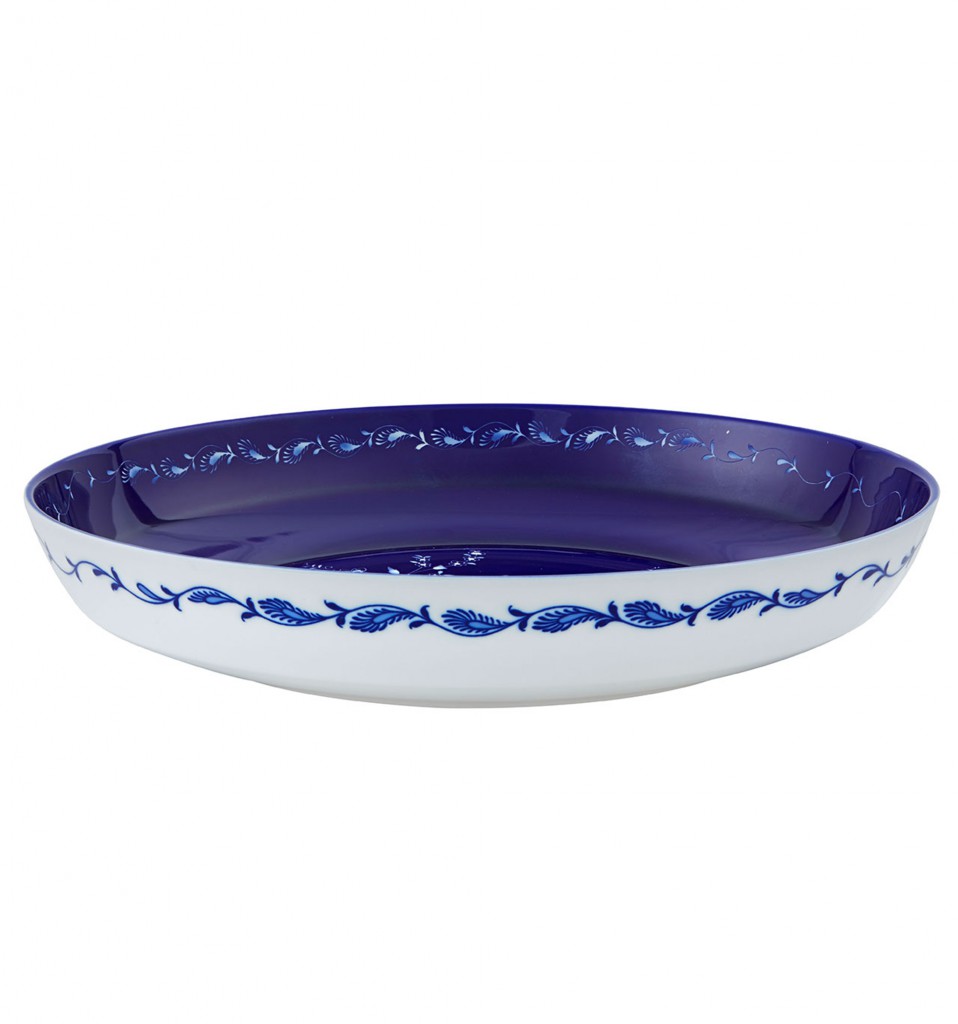
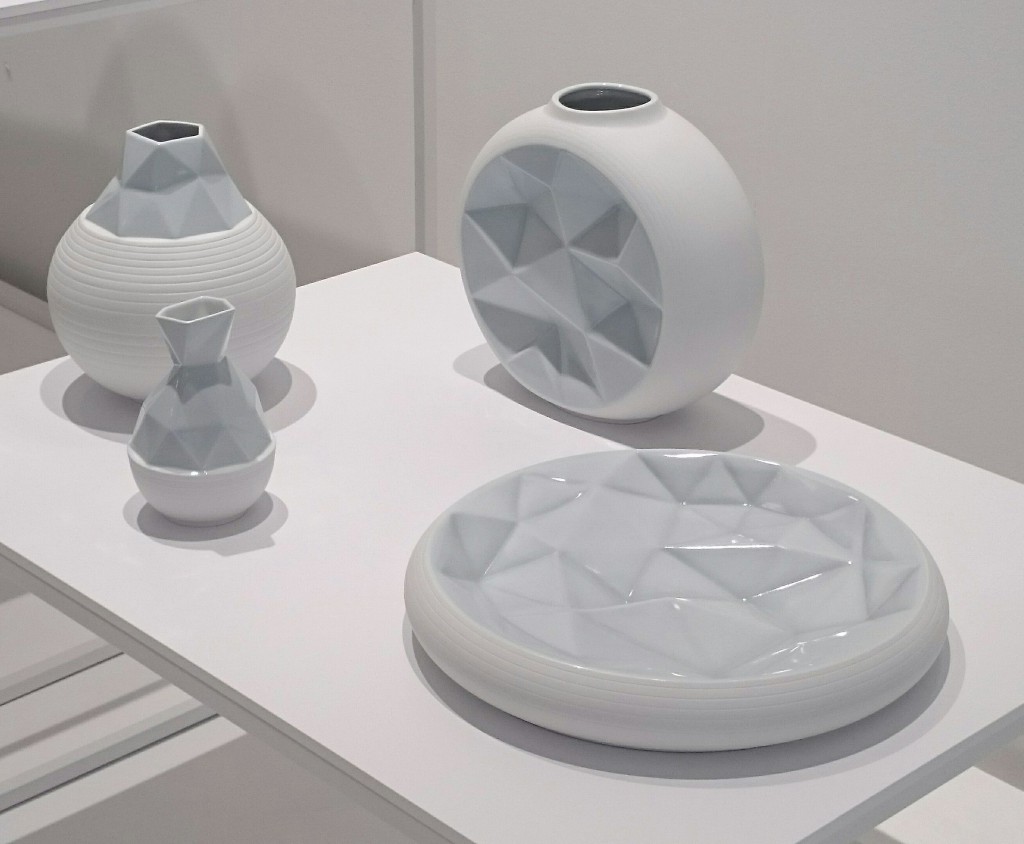
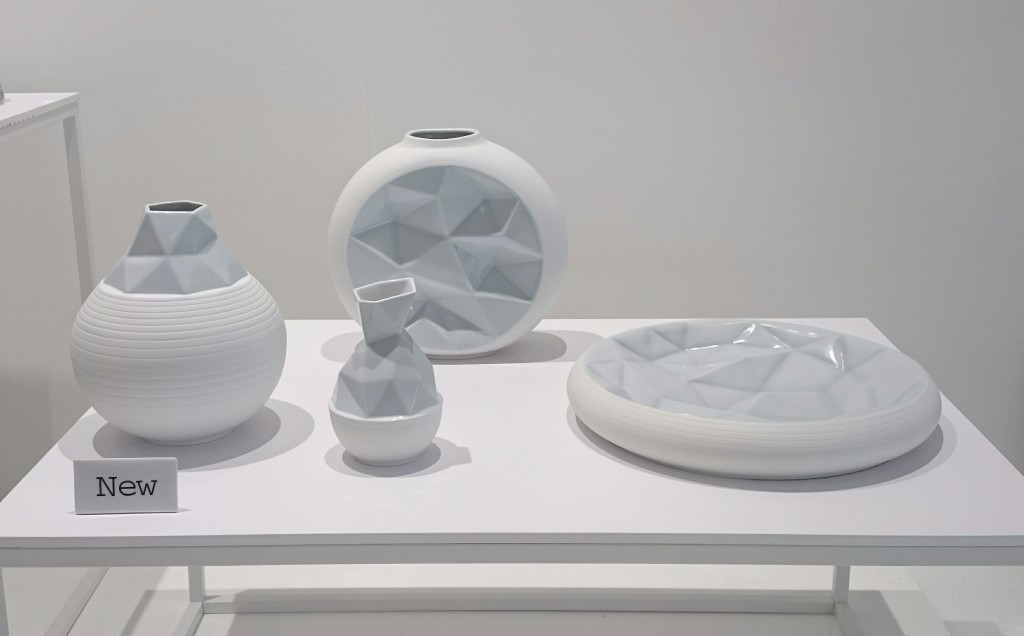