Olivier van Herpt Cracks the Porcelain Code
Olivier van Herpt has developed a new 3D printer that allows the artist to create large-scale porcelain works that push past previous possibilities of this ancient medium.
It took three-years and twenty-six attempts before Dutch designer Olivier van Herpt succeeded in his mission of creating perfectly thin, light-weight, large-scale porcelain objects that measure over 1-metre in height. To understand the artist’s determined focus to achieve this unusual yet remarkable success, we need to go back in time, to when van Herpt was graduating from the Design Academy in Eindhoven. Ten years ago, while finishing his studies, he invented a 3D printer that worked with traditional modelling clay rather than the conventional plastics of the time. As he explains, “This allowed me to experiment with many clays, from terracotta and stoneware to porcelain. Over the years, I constantly improved my machine to unlock uncharted possibilities in these materials in terms of forms, textures, and colours, showing that, despite its long history, the millennial medium of ceramics still has so much to offer.”
About five years ago, he was confronting issues with the limitations of porcelain, which, unlike other clays, softens in the kiln. As he made larger objects, he found they were constantly collapsing under their own weight, causing cracks and deformations. Researching solutions to this problem, he discovered that there was not one. Instead, artists had adapted and made compromises, either by reducing scale or by adding in normal yellowish stoneware clay and then covering it with white glaze or engobe to resemble porcelain. But rather than accept and adapt, Herpt took this on as a challenge.
“I didn’t want to let porcelain surrender to this fate; I wanted to bring porcelain to new heights without those compromises that had to be accepted until now. I instead wanted to keep the essence of the material and liberate it from the constraint of the round form.
Therefore, I started improving and tuning my machine to be able to form extremely thin porcelain. Porcelain pieces thinner than ever before perfectly survived firing undamaged, because of their exceptional lightness. The machine now allowed me, for the first time ever, to venture into new forms previously deemed impossible at a large scale.”
Van Herpt was interested in creating asymmetrical, unbalanced and dynamic forms to show what porcelain was capable of bringing, despite over 1000 years of history telling him otherwise. As van Herpt explains, “Porcelain doesn’t accept mistakes.” There were mathematical concerns as well, such as the fact that the larger the porcelain object, the more it shrinks when fired. Therefore, he had to scale bigger in order to achieve the height and volume he wanted.
“I had to not only implement my machine for forming but also developing techniques for drying, firing, colouring, creating new tools for these phases too. A piece doesn’t survive firing solely because of the machine. The machine is a necessary but not sufficient condition for the piece to have a chance to exist. The machine allowed me to enter the uncharted territory of large porcelain, but there is a complex process behind the success of a piece; every step in the long process of working with porcelain has to be functional for firing.” The result of this investigation is Dunes, a series of tall standing blue and white vessels that delicately twist and spiral upwards.
Van Herpt is giving a good name to the possibilities of using not just technology but AI in creating crafted objects. He reveals how
it can be a tool to achieve new levels in a material and that it can remain beautiful and truly unique and reflective of the artist’s vision. “For me, my machine should never be the limitation but an enhancer, never finished but always in development, to expand the possibilities of the medium. Each time a limit is overcome, it leads to encountering a new one to be surpassed. I believe ceramics still have so much to offer, and I put for the first time the tool at the command of the material rather than limiting the material to the capabilities of the tool. I see it as the best way to use the technological advancements we have available.”
What’s next for the artist? More experimentation and exploration. “I am going to continue my exploration in large porcelain until I find a new limitation. When a limit finds me, an object finds me.”
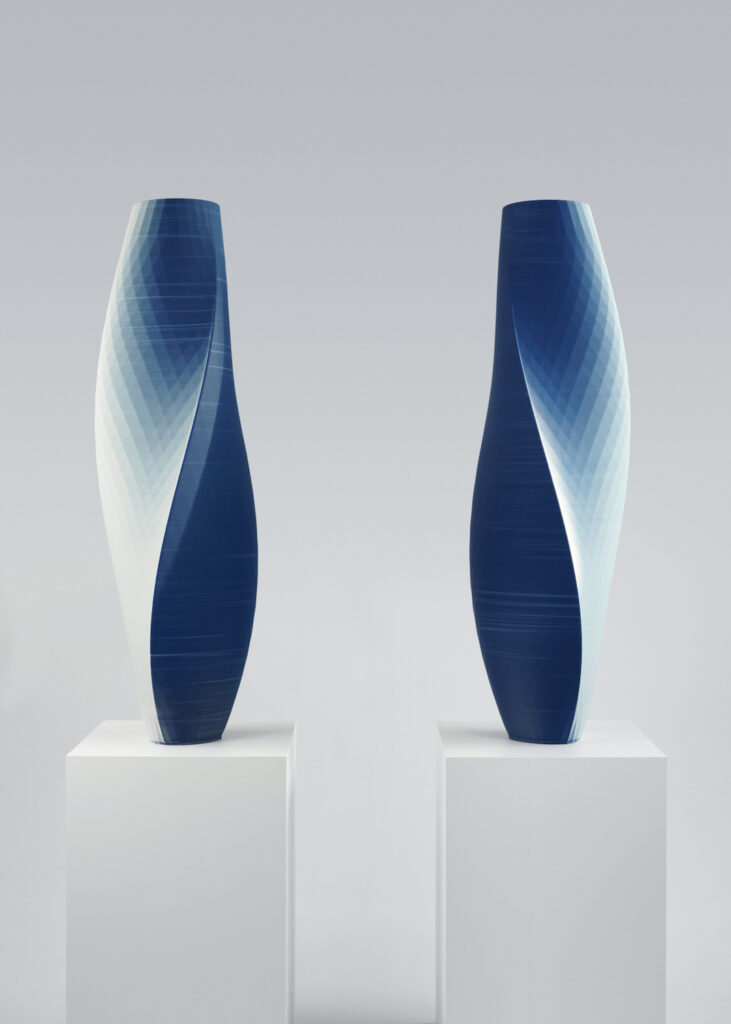
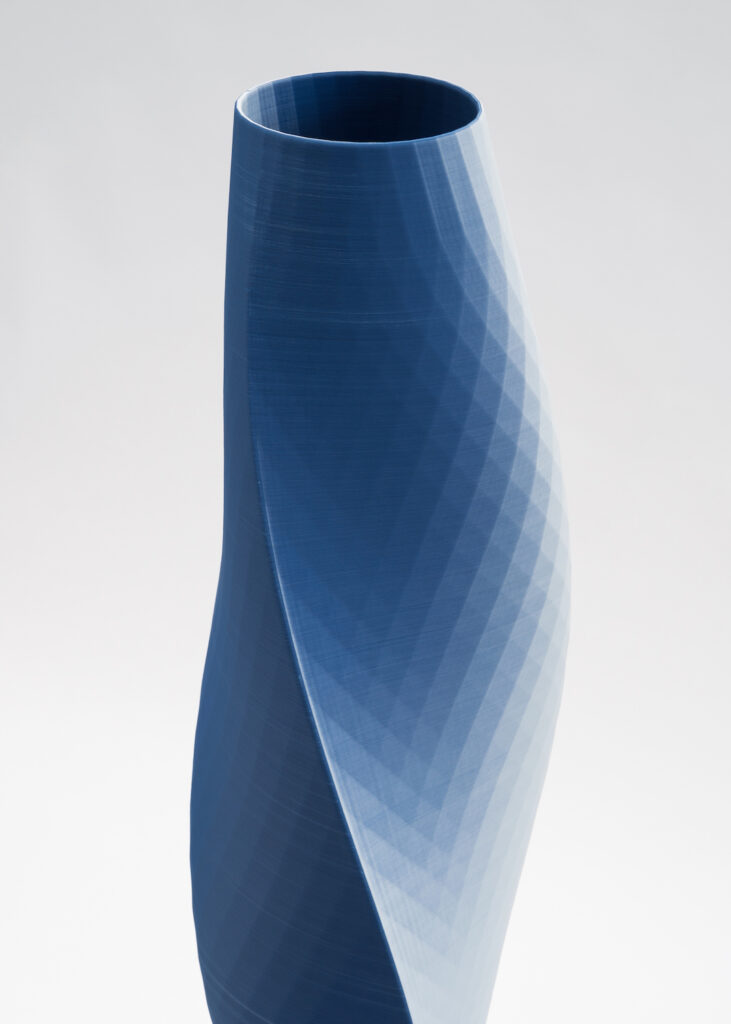
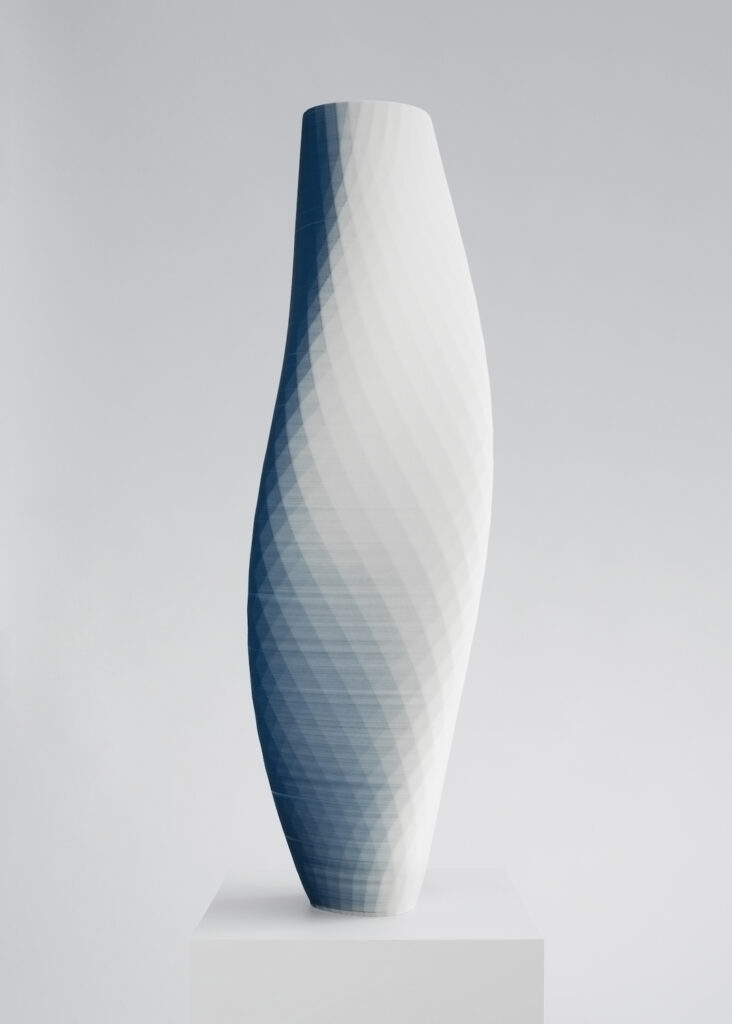
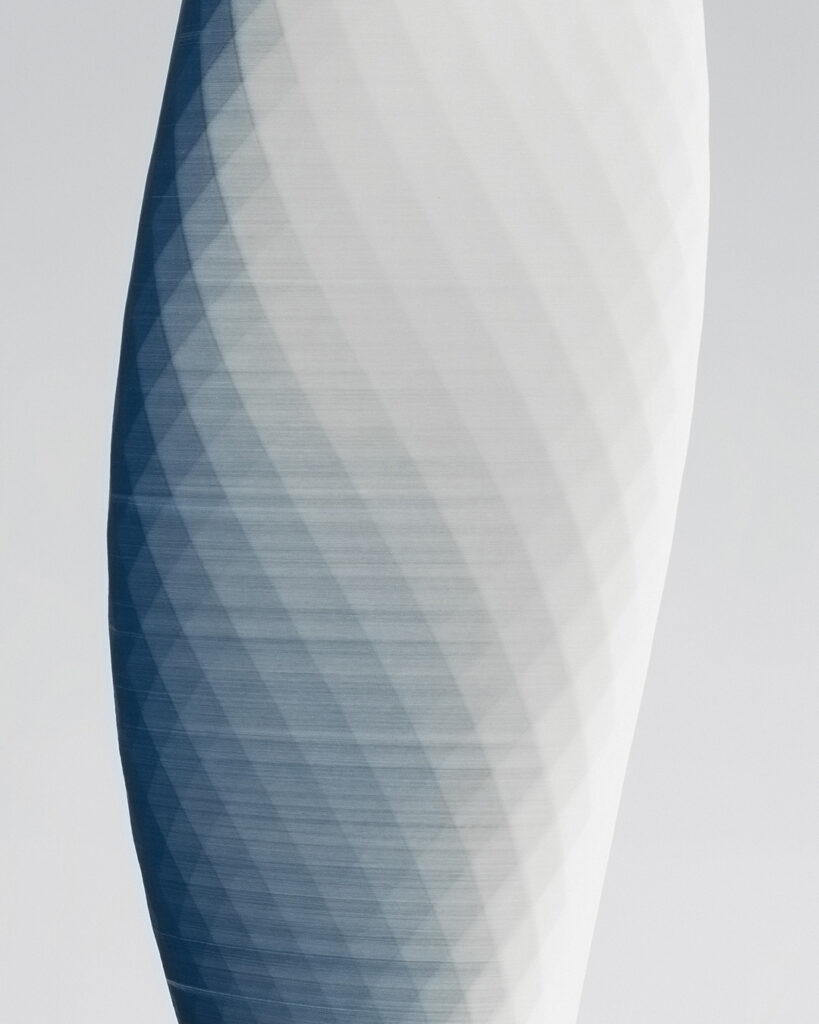
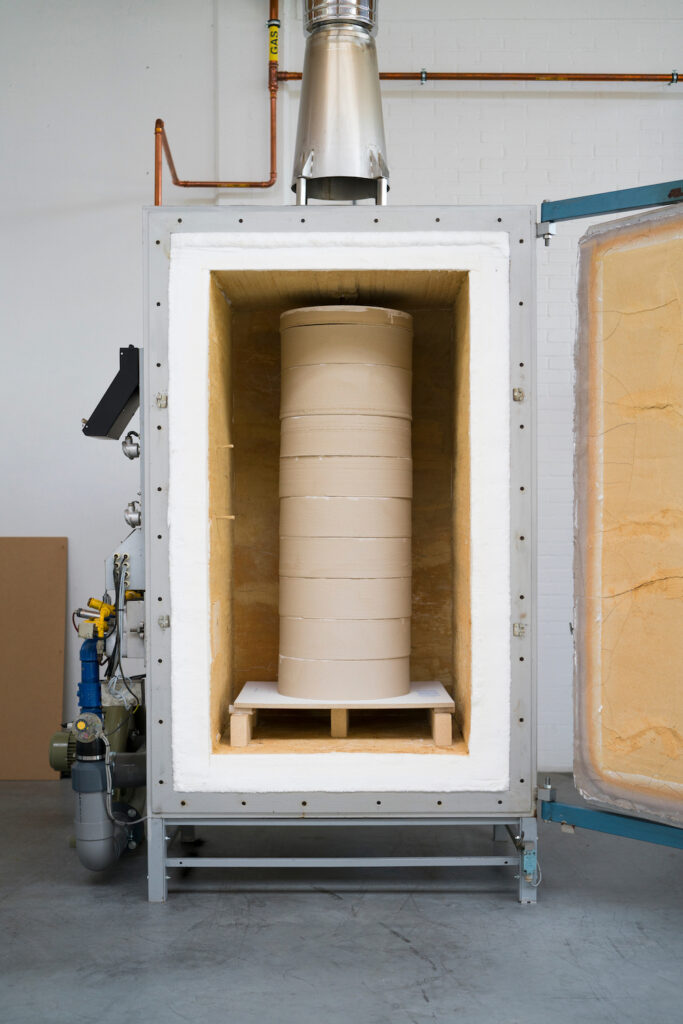
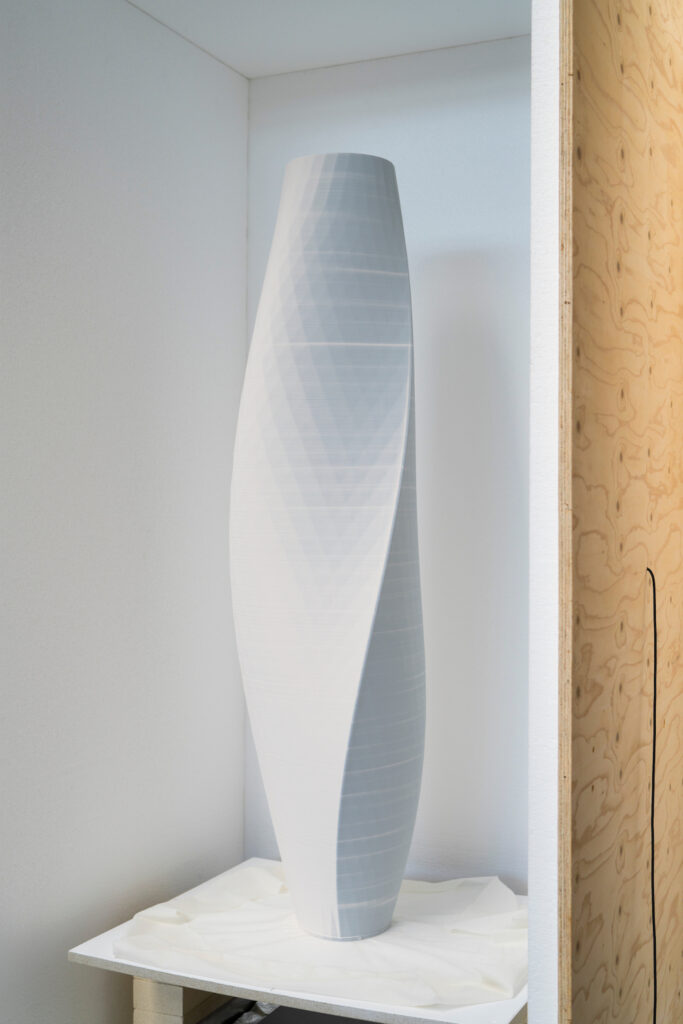
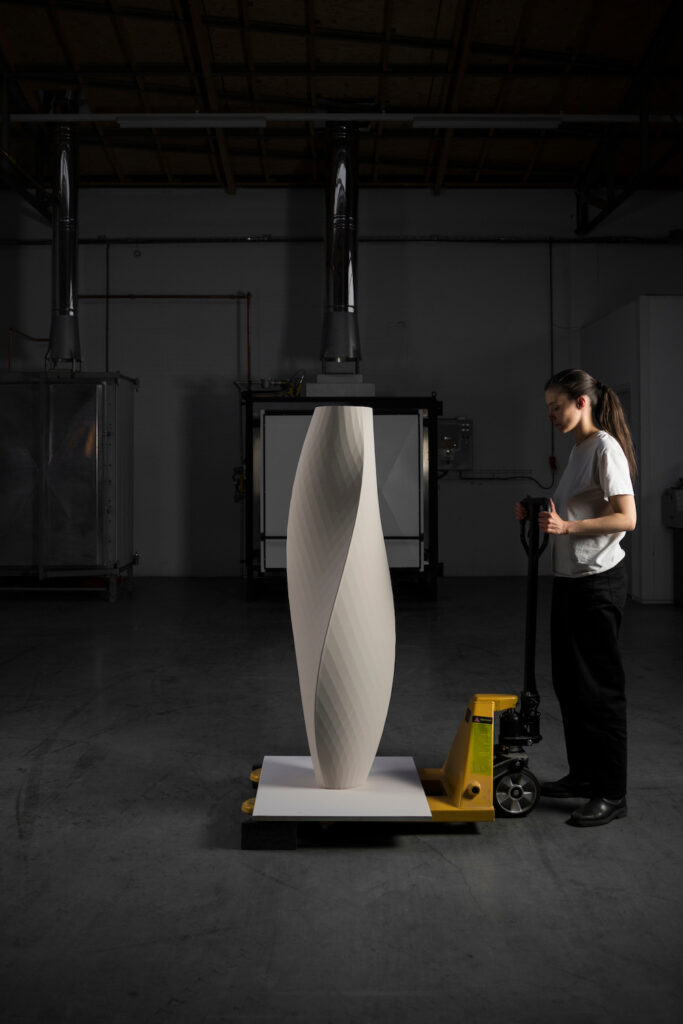