Material Tendencies: Färg & Blanche
Fredrik Färg and Emma Marga Blanche like to combine industrial production and exclusive handcraft. The works of the Swedish-French design duo often have a tailored, yet playful, touch – showing that their experiments, in particular in textiles, could be applied to mass production.
Architonic met Färg & Blanche in Milan and discussed their hands-on experimentations with materials.
Anita Hackethal, Architonic: If you had to pick one material to work with for the next three years, what would it be?
Fredrik Färg and Emma Marga Blanche: Textiles. Because there is a lot of innovation happening. You can go from being flat to having volume – you cut, you shape, you tailor, you construct. It can be used for many different things. The more we work with textiles, the more we get into the material. It is fascinating in every way. You can also make self-supportive structures today.
AH: You’ve executed many projects that involve textiles, using different techniques and partly placing textiles in unusual contexts. Could you mention one project that has stayed in your mind and share your experience with us?
FF & EMB: I think it would be the Emma Armchair for Gärsnäs. It is a hand-sewn, well-tailored armchair that speaks the language of craftsmanship, picking up the gauntlet. Our idea was to stitch right through the backrest of the armchair. There is no wood or metal frame in the backrest, only a textile composition. The material for the backrest is piled up in layers and then sewn together in one move with a sewing machine. It is an effective production, but takes a very skilled craftsman to make this chair.
AH: What role does material play for you in the design process?
FF & EMB: Our ideas don’t always start with the material, but in some way our design process is materially driven, and production methods usually play the central role in our projects. We like to work with different materials using mass production methods, where you can see the touch of the hand. As Fredrik has a background as a cabinet-maker, he tends to think a lot about the materials and construction context, whereas I, Emma, think more about the conceptual context and why we’re doing something.’
AH: Is there a material with which you don’t have quite so much experience but would like to explore a bit further?
FF & EMB: We’re always curious about new materials. We have little experience with ceramics and would love to develop further in this field. Also glass would be a wonderful material to work with, which we haven’t so far. As for textiles, we’ve noted a large development in 3D knitting – everything from shoes and clothes to furniture. For future projects, we have been experimenting with natural fibre, for example linen and hemp. We think that textile or fibre material will be seen in a range of appliances. You can already see this happening in the car industry.
AH: With your Wood Tailoring Collection, you stitched directly onto layers of plywood – sewing technology was taken to its extreme. How did you come up with the idea? And how was this different to sewing/working with textiles? Please tell us about the challenges?
We started experimenting with extreme sewing a long time ago, maybe 10 years. We broke several sewing machines, continuously trying thicker and harder material and creating textile compositions, like we did for the Emma or the FAB chair. Finally, we invested in a new industrial sewing machine to have more possibilities. Sewing into wood veneer was something that we also started many years ago. But stitching into thick plywood was a new challenge and after a year of testing different methods we were finally able to control the technique and presented the first collection at the Stockholm Furniture Fair in 2014. Nobody believed that it was possible to use wood tailoring for mass production, but we’re now working with producers to develop new products with this technique.
This article originally appeared on Architonic, where TLMag presents articles in French and English.
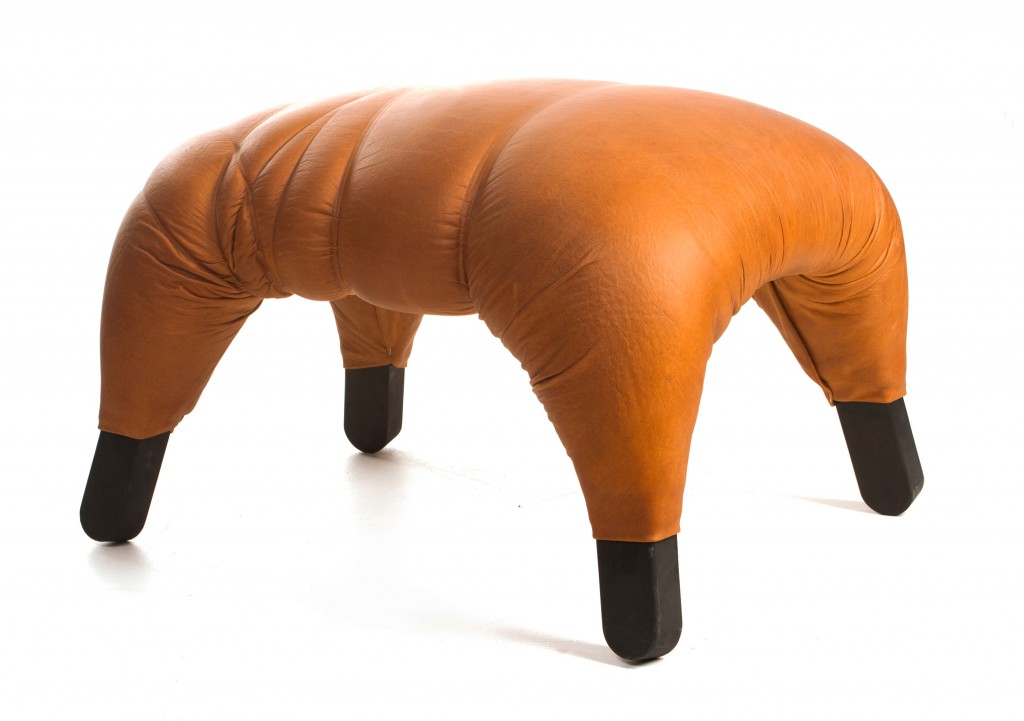
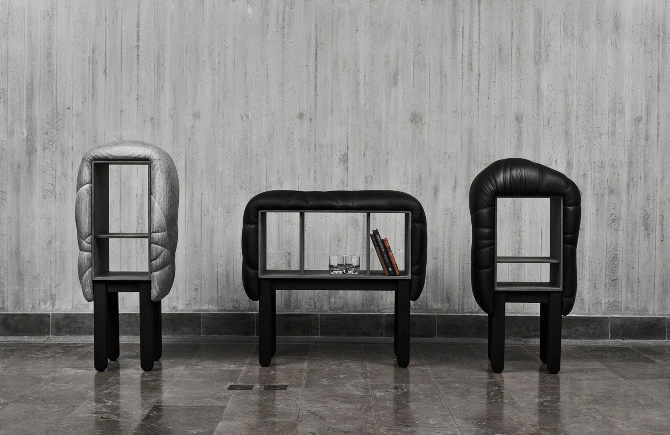
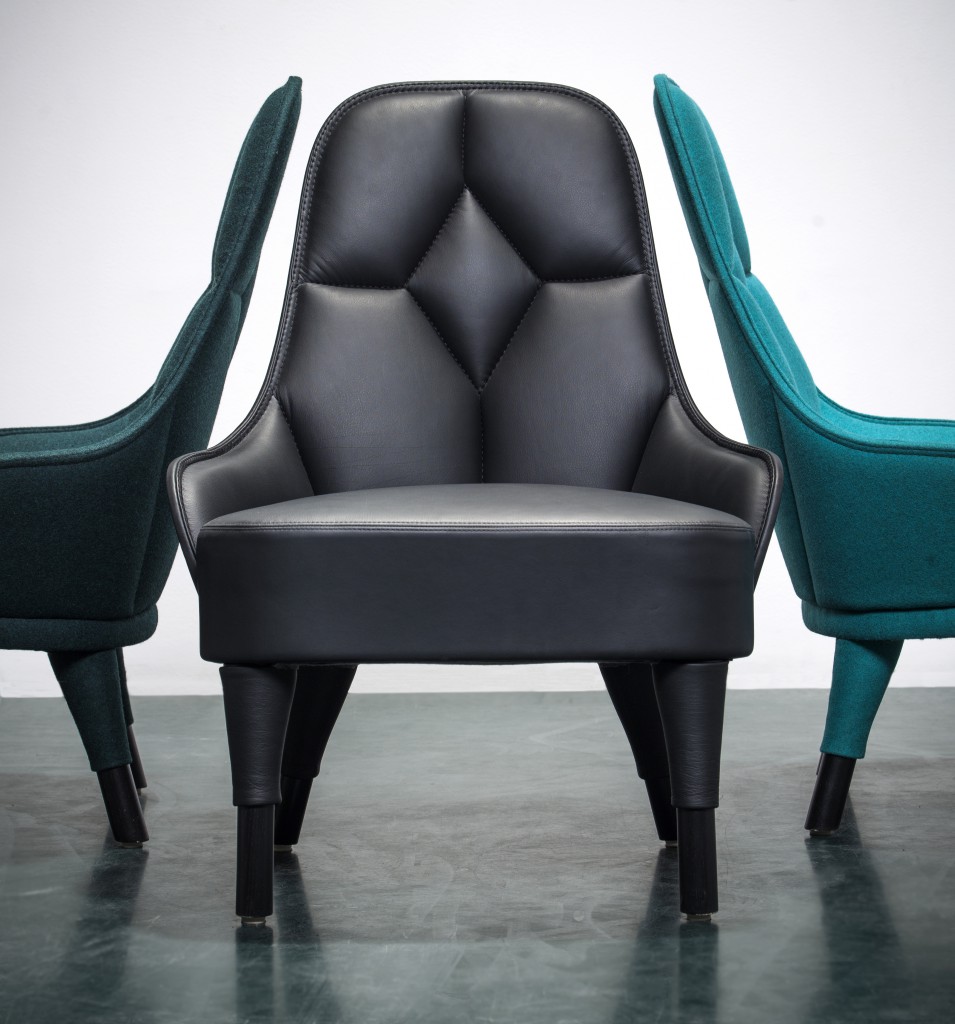
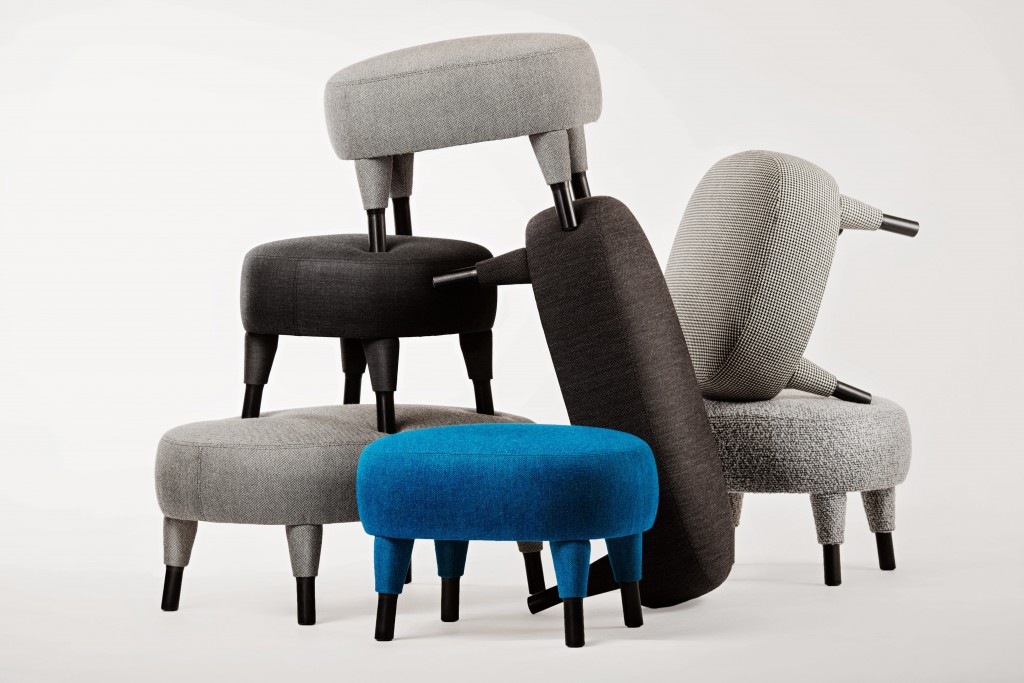
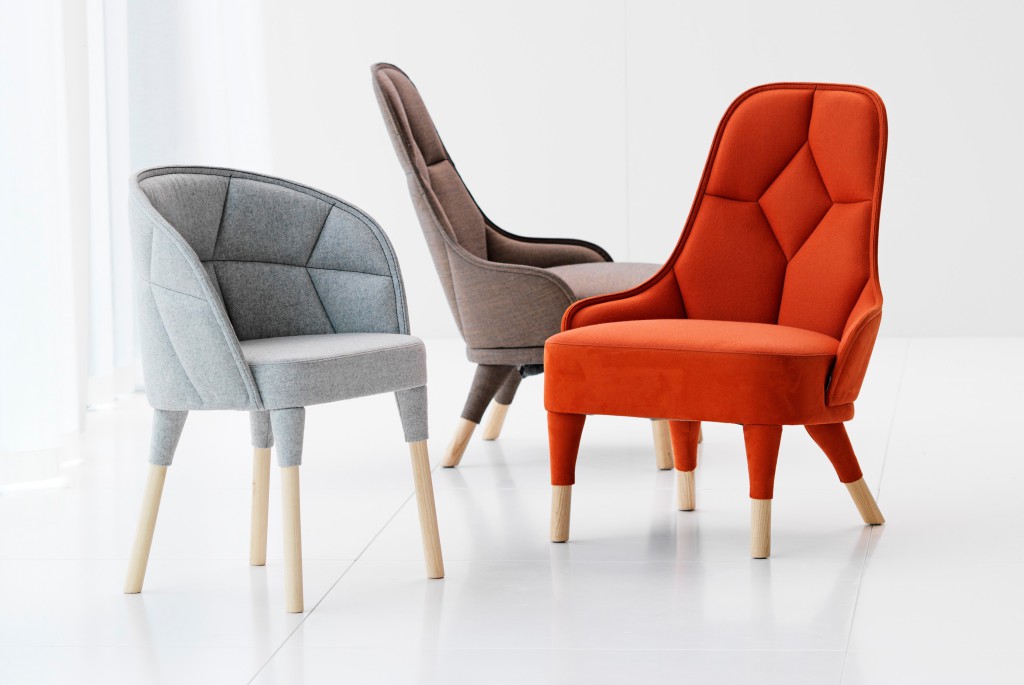
![Fly F-A-B chair special Clément Ader. The Fly F-A-B chair is an interpretation of the well known bat-alike aeroplane Avion III, which was created by Clément Ader, a French engineer and explorer. The piece was specially made for the exhibition 'Design [R]evolution at the Musée des Arts et Métiers' in Paris.](https://tlmagazine.com/wp-content/uploads/2016/09/fargblanche_material-tendencies_fab_fly_chair_architonic-1024x835.jpg)
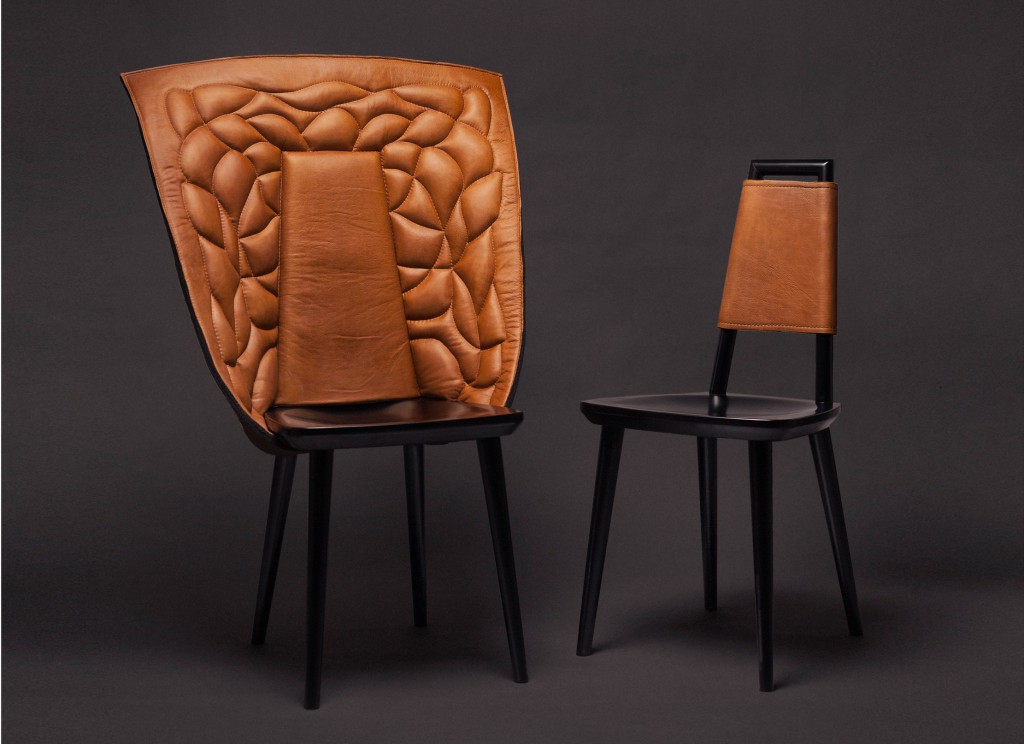
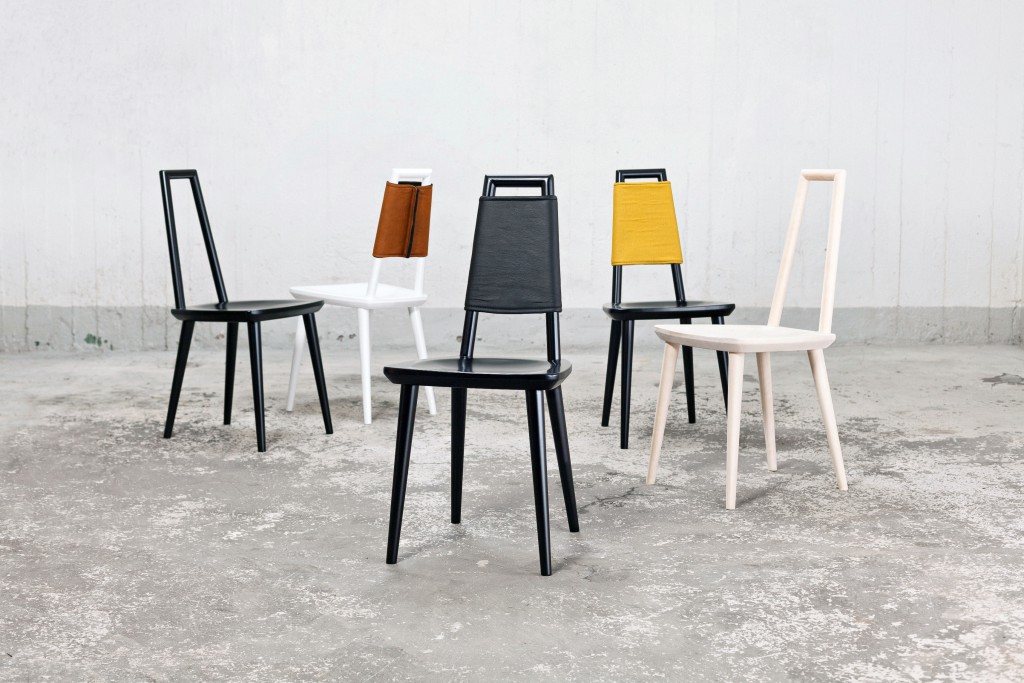
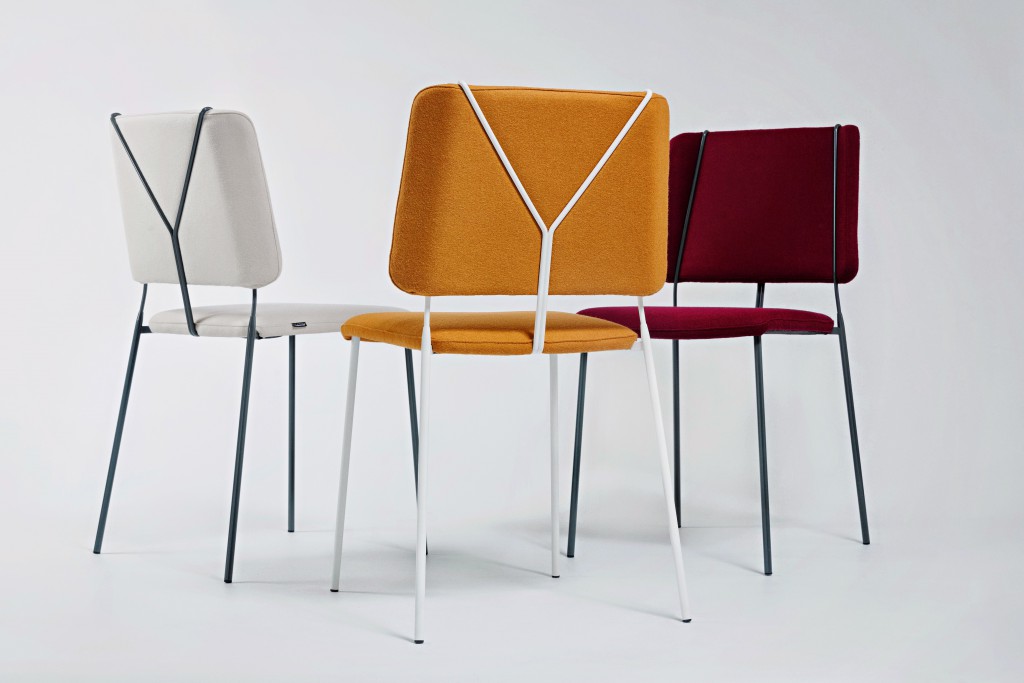
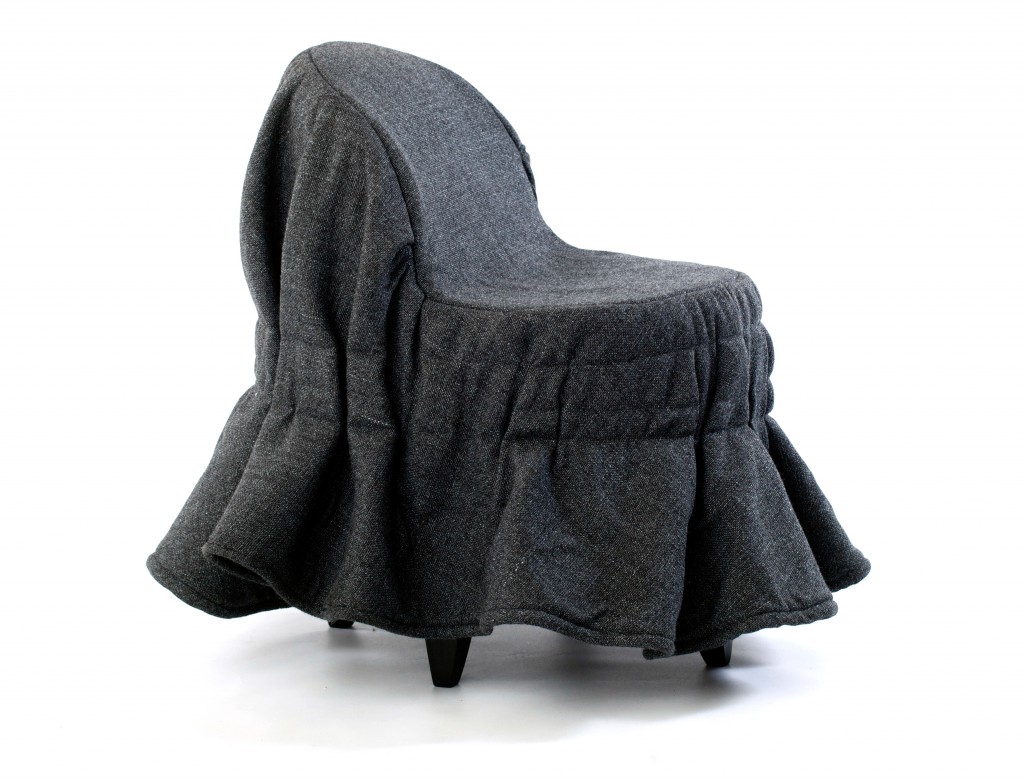
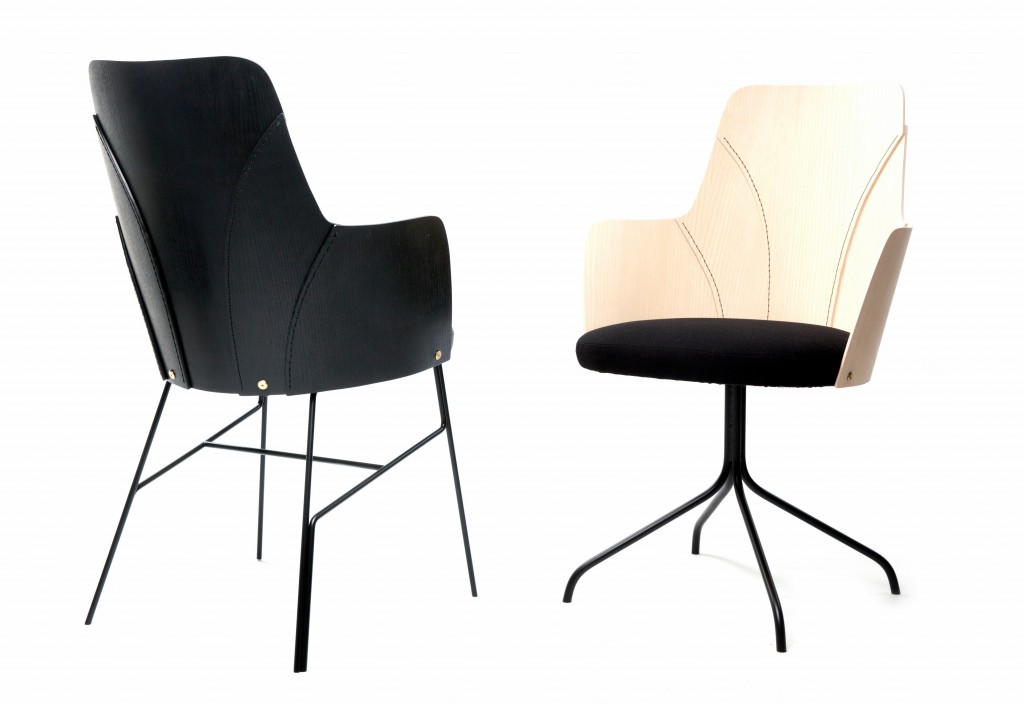
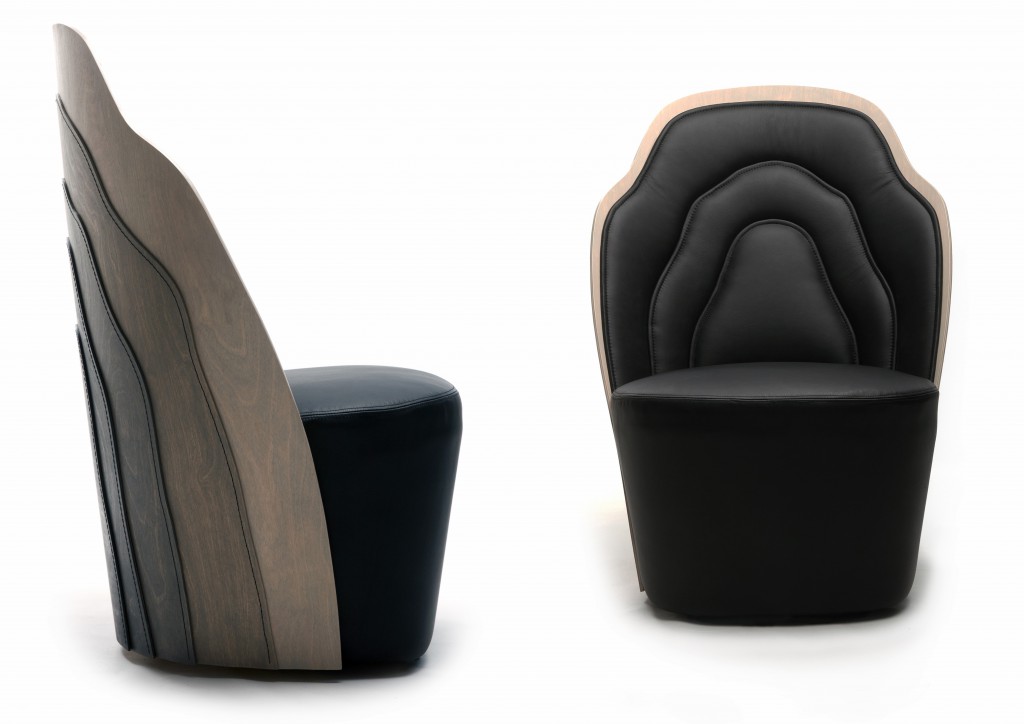
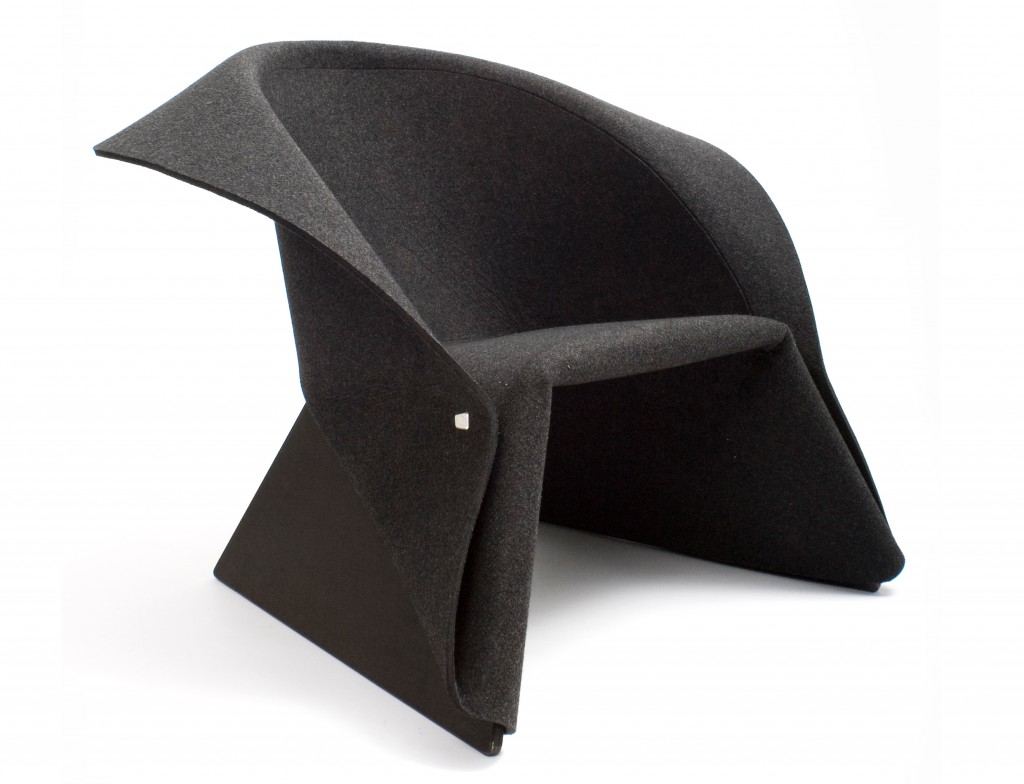
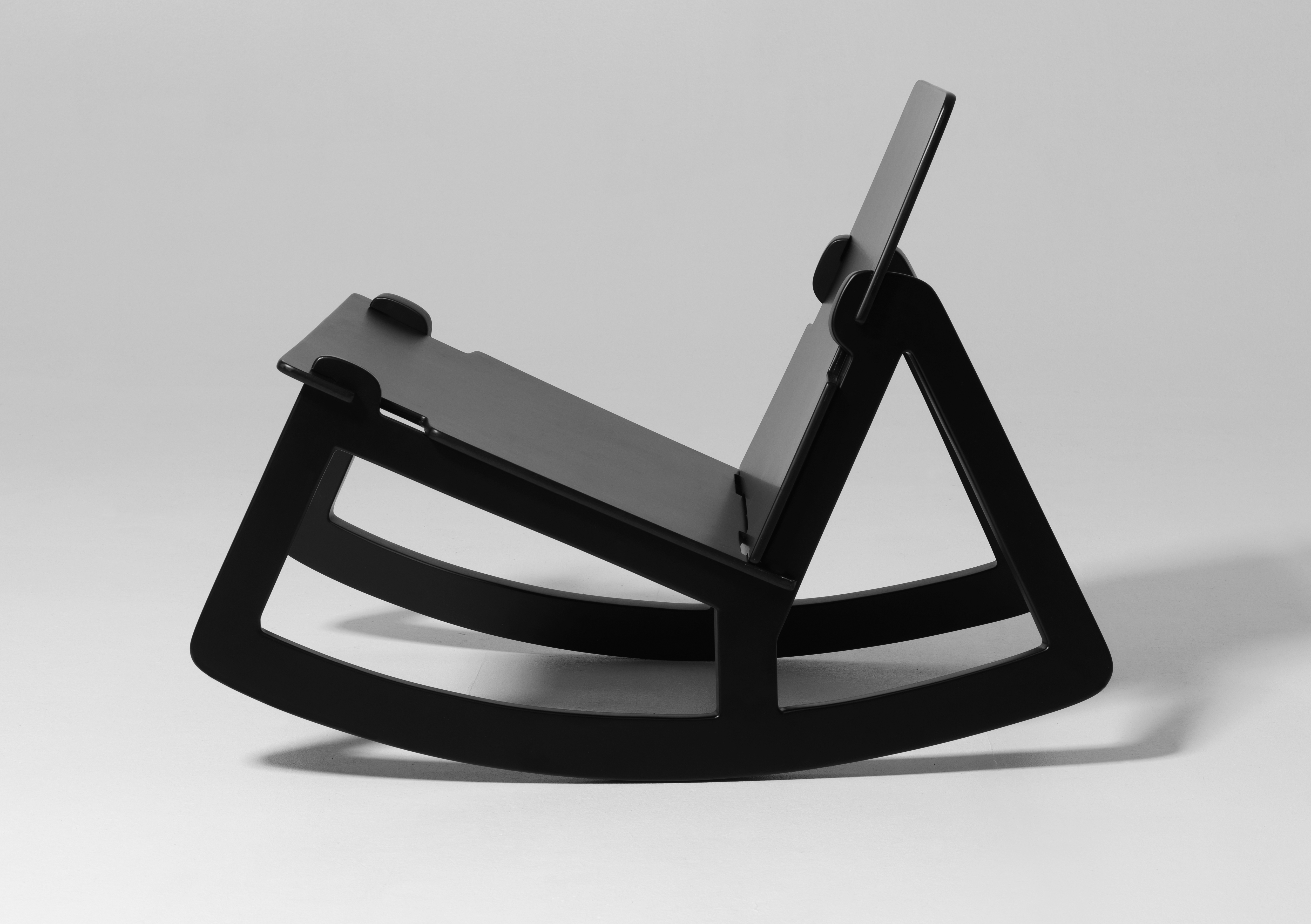
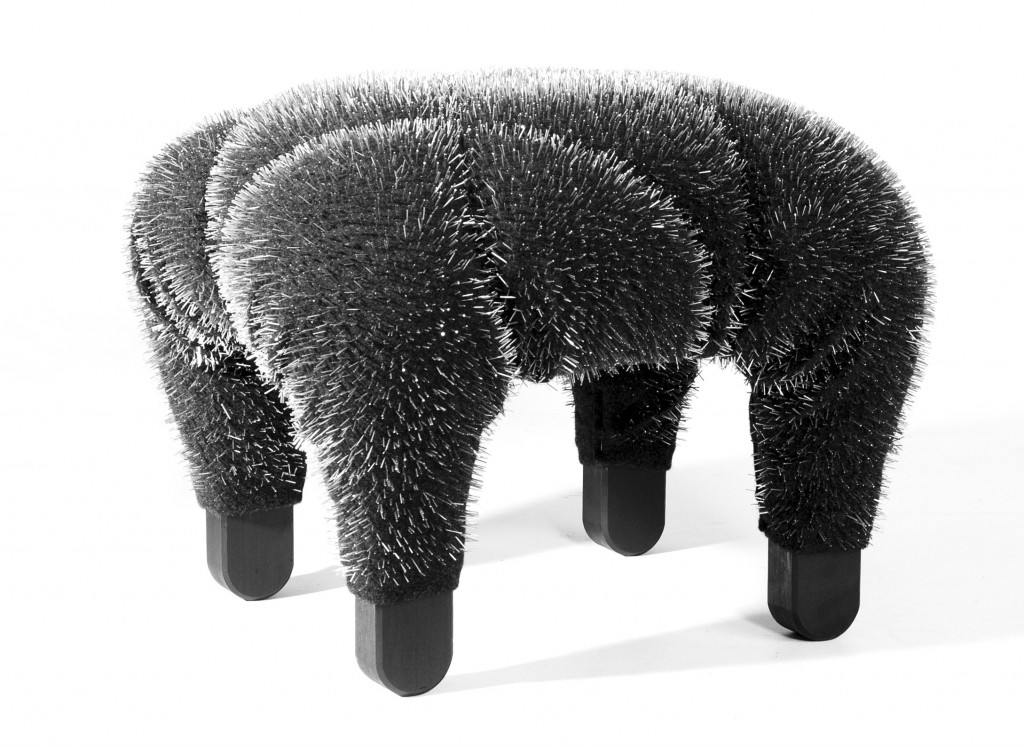
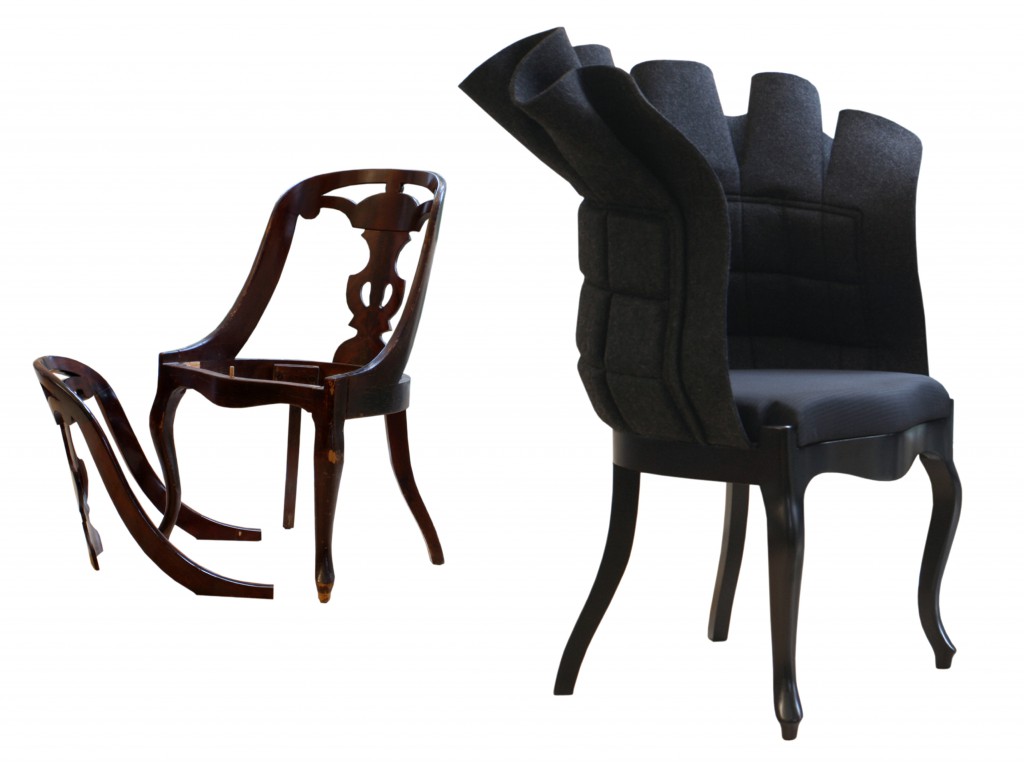
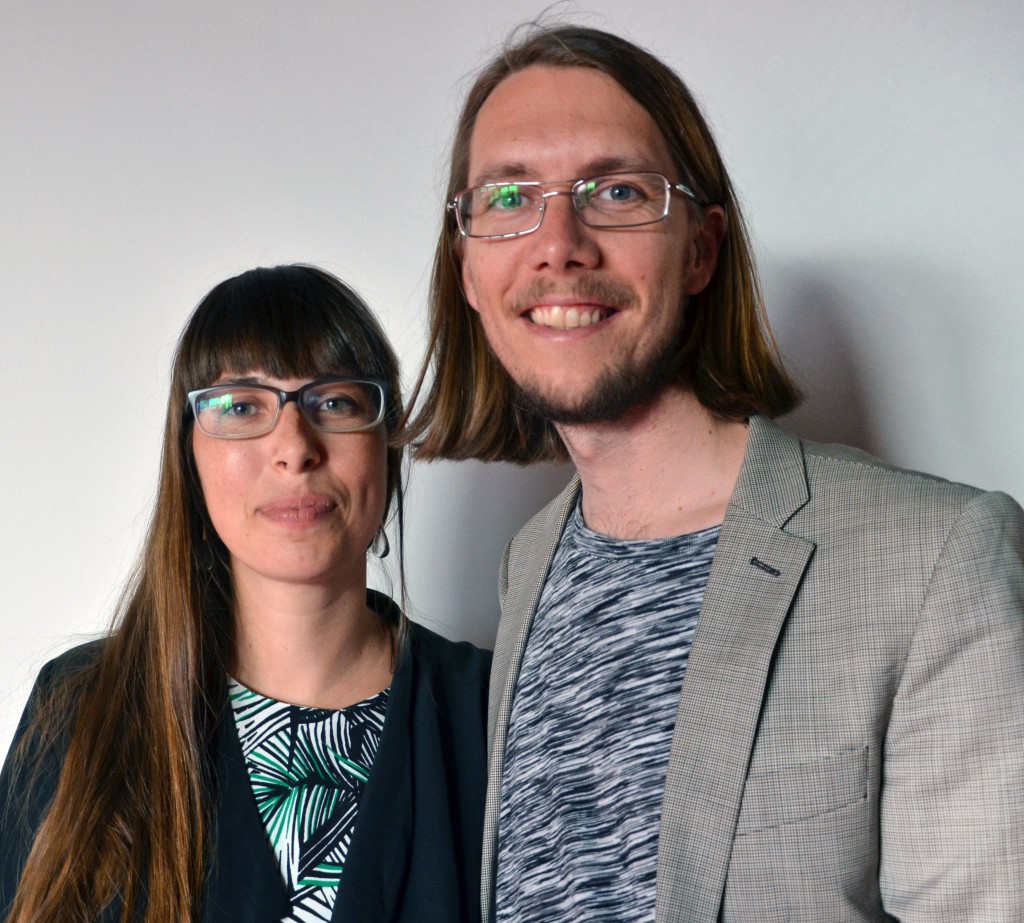