Material Tendencies: Michael Young
Looking for a new journey, Michael Young moved to Hong Kong in 2006 where he was quickly intrigued by the highly evolved engineering skills and manufacturing opportunities. With a spirit of industrial adventure, the British designer likes to explore the facilities of the local factories and pushes its traditional techniques to new limits.
Architonic met Michael Young during the London Design Festival to speak about his passion for pioneering technology.
Anita Hackethal, Architonic: If you had to confine yourself to a single material for the next three years, which one would you choose and why?
Michael Young: “I think it would be injected anodized aluminium foam. It is a process that architects have used before and I’ve been developing it in Asia during some exhibitions for around the world. So I started making it myself by creating my own tooling, injecting aluminium with gas, 800 degree Celcius. I think it got plenty potential to keep me excited for three years. There is enough flexibility in the material. So yes, it could keep me entertained probably even for the rest of my life, to be honest.
Aluminium is one of the materials that Michael Young has focused intensively on. The Chair 4A for EOQ is made using extruded and stamped recycled aluminium. He captured the engineering skills employed by local industry and puts that depth of knowledge in aluminium research into furniture design. The chair comes in six different finishes including anodised, powder coated, and polished aluminium.
Starting with the same extrusion process, the soft forms of the dub pendant lights for EOQ were sculpted by removing much of the aluminium material. This allowed encasing the resultant space in hand‐blown glass vessels produced in the Czech Republic. The extruded aluminium fins, combined with the glass, allow light to be diffused, creating an ambient glow.
AH: Is there a material that you could immediately reject?
MY: No, I think all materials are interesting. It really just depends on the sort of context with which you use them, quite frankly speaking. I have always found plastic quite challenging, mainly because it doesn’t age particularly well. But I understand its functionality, which is pretty much the only reason why I never designed an all in one plastic chair. Though, as time goes by, my interest in doing that ‐ regardless of that concept ‐ is growing stronger. So every material has its place.
AH: Besides designing for companies, do you also produce yourself?
MY: I started off making things in workshops over 23 years ago, so being hands on or getting dirty in a workshop is not something I’m afraid of. Though the only things I produce myself are really the editions that I put up in art events, so to speak. Having the opportunity to do work in galleries or like what I did last year at the FOG art fair in San Francisco helps me return to the real reason why I started design, and that is because I can make something. It is a bit like cooking ‐ you get an instant response to it. That sort of gratification is quite nice from time to time, because traditionally design takes a year or two to get an object from start to finish. At the end it is design as industrial art that interests me most, but on a scale of mass production.
This article originally appeared on Architonic, where TLMag presents articles in French and English.

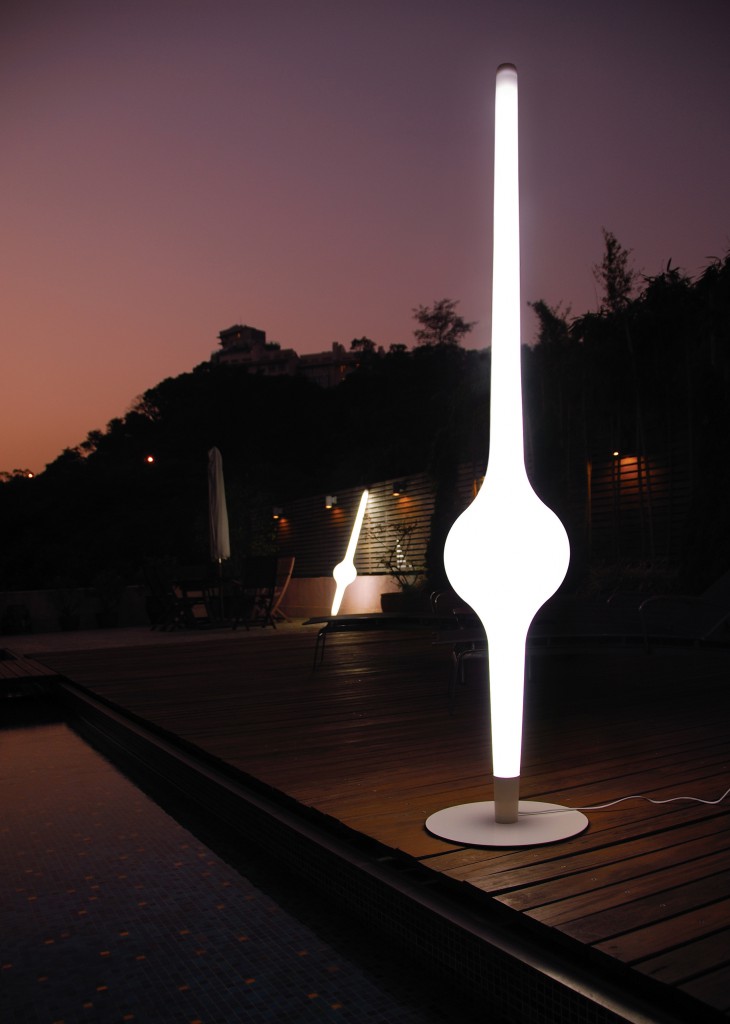
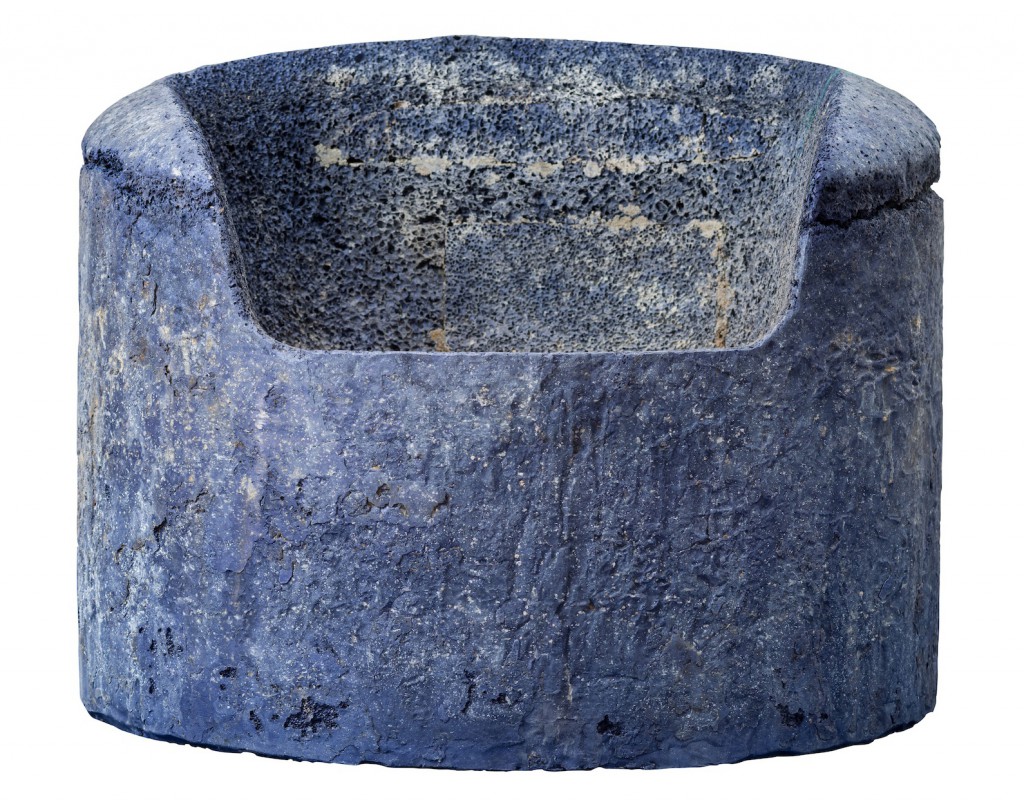
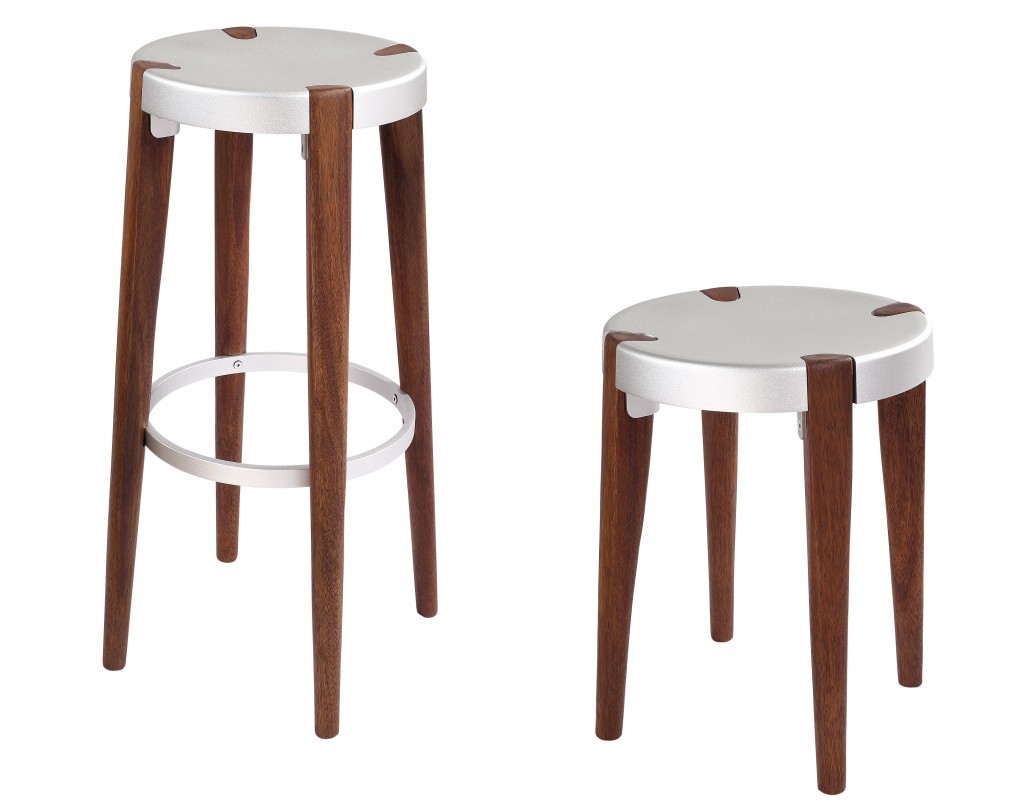


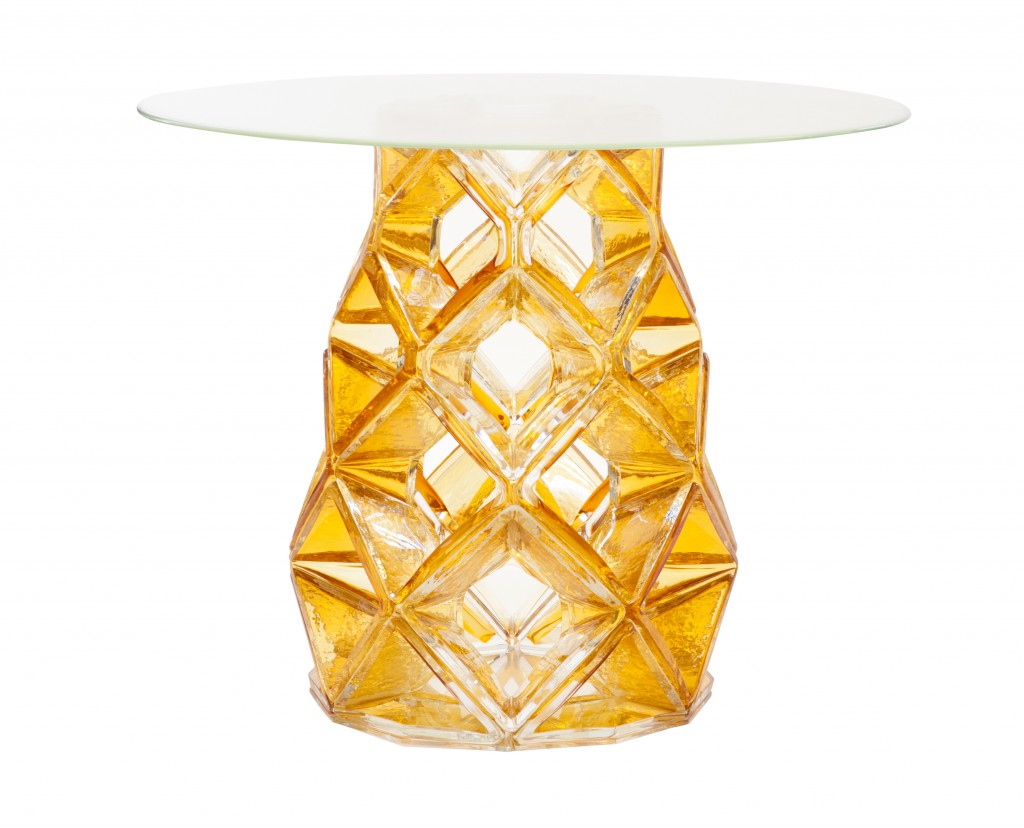
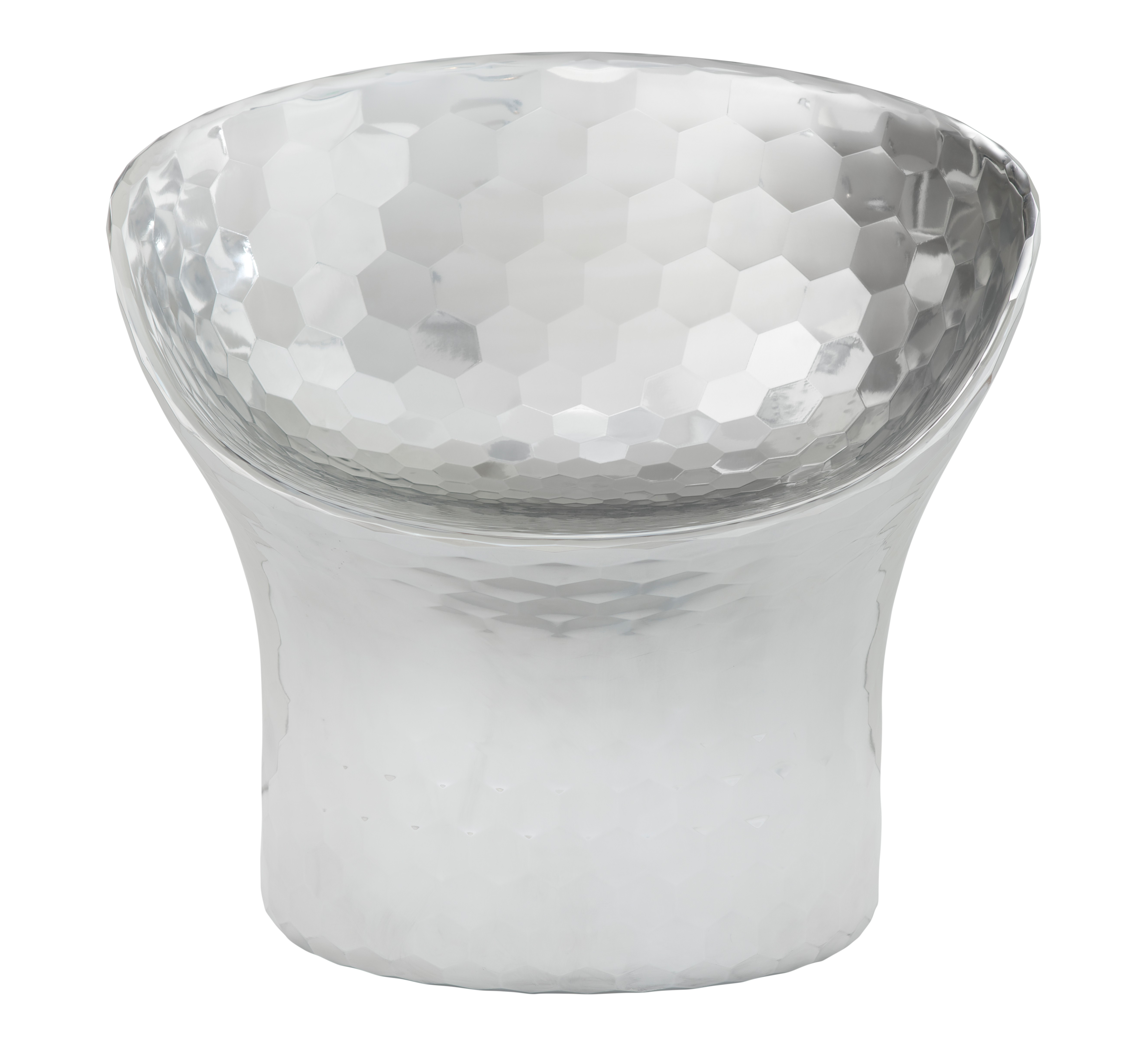
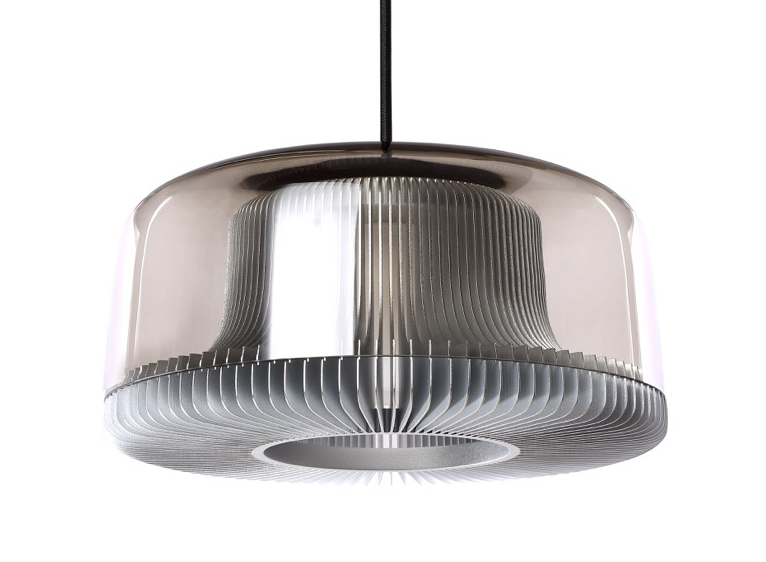
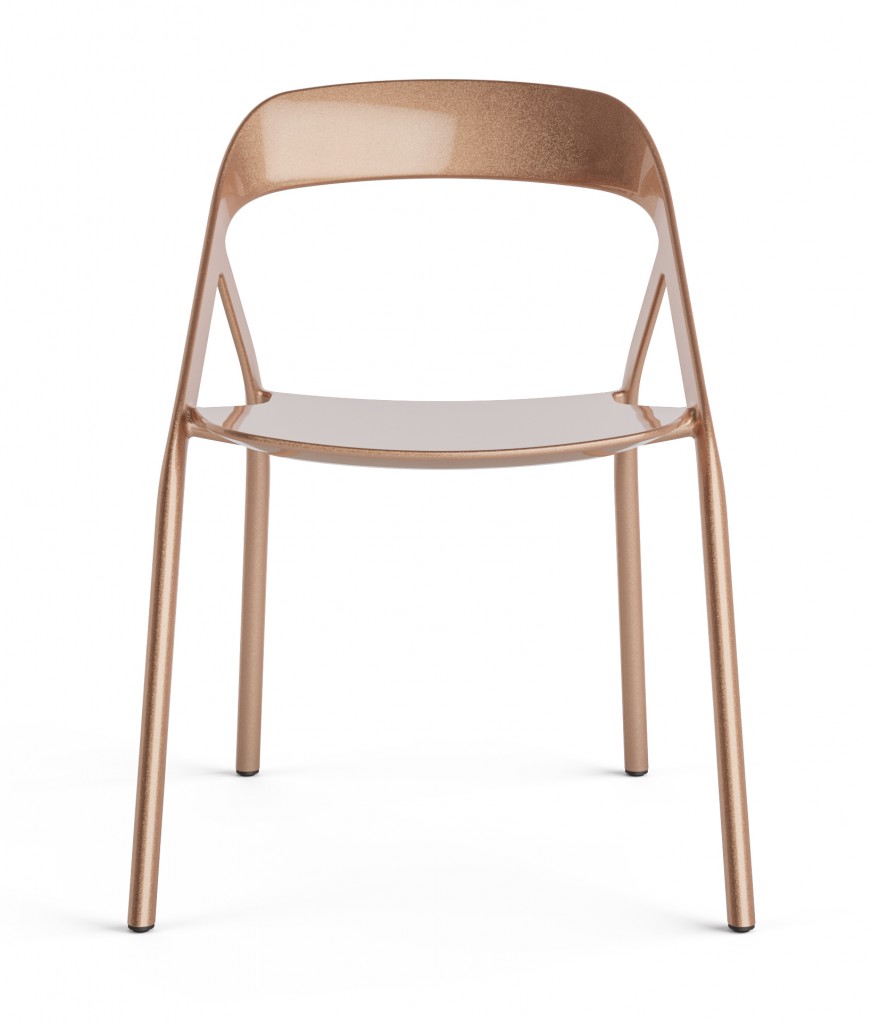
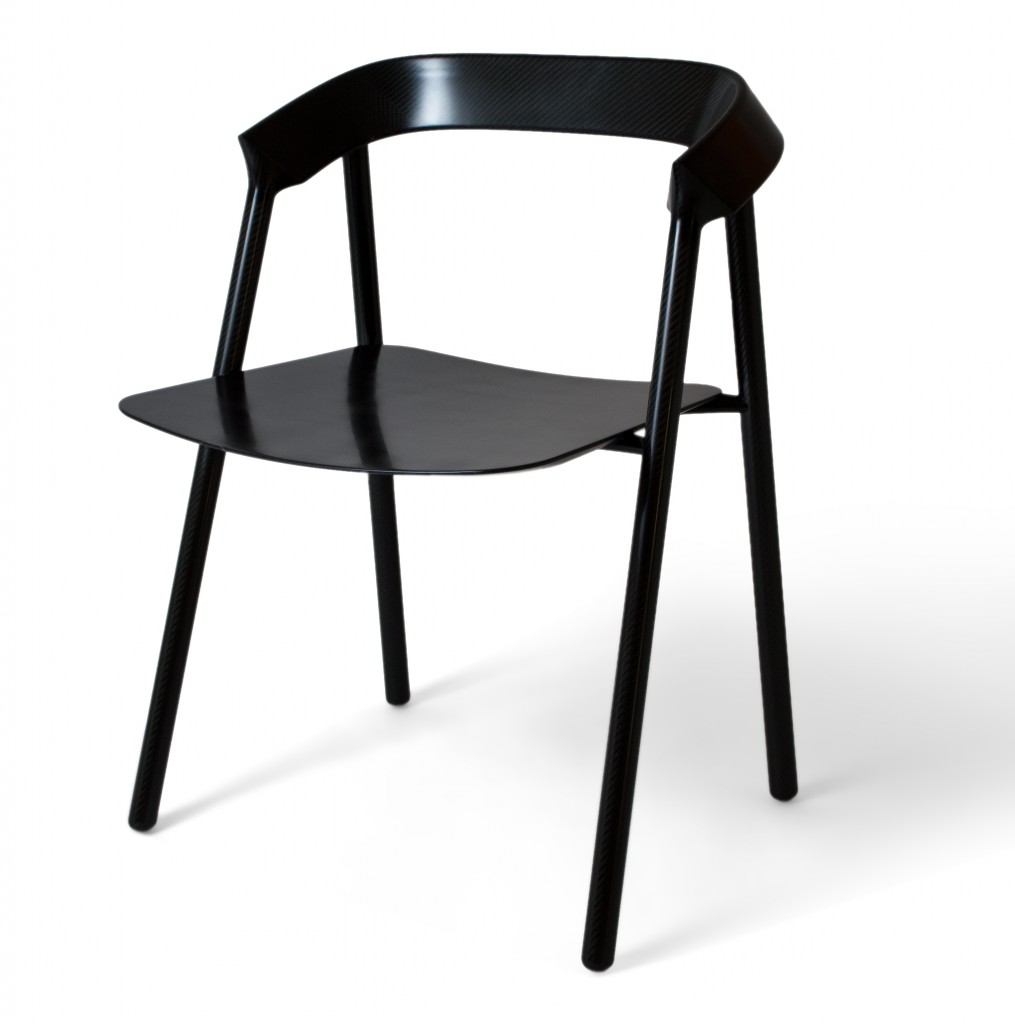
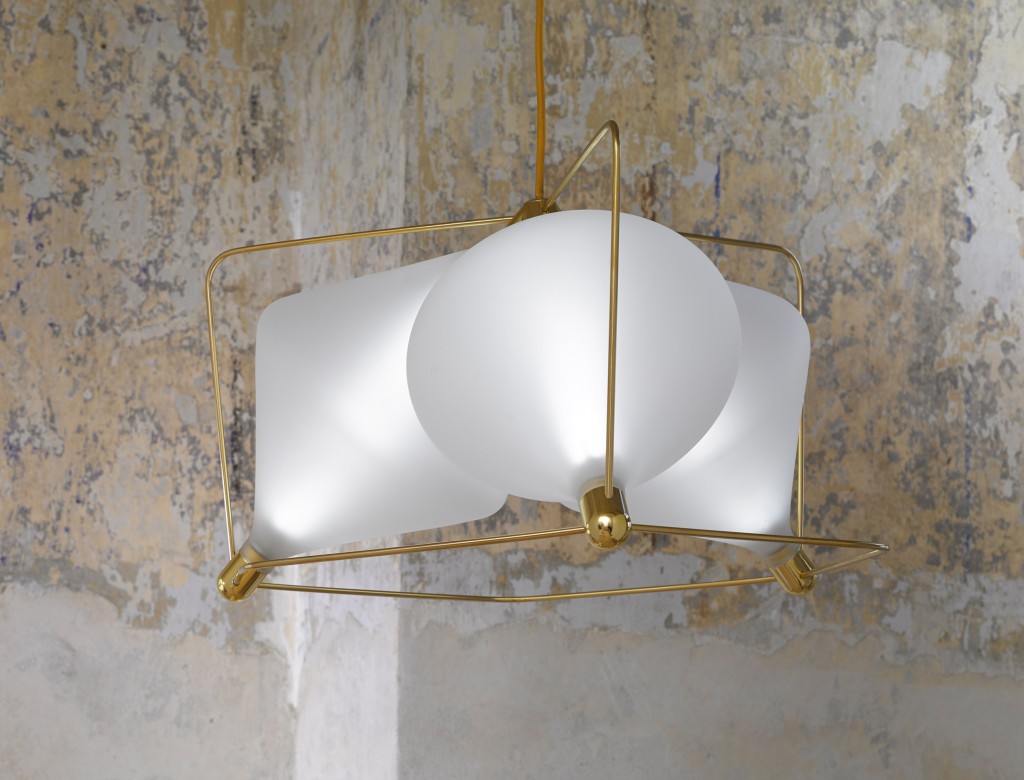
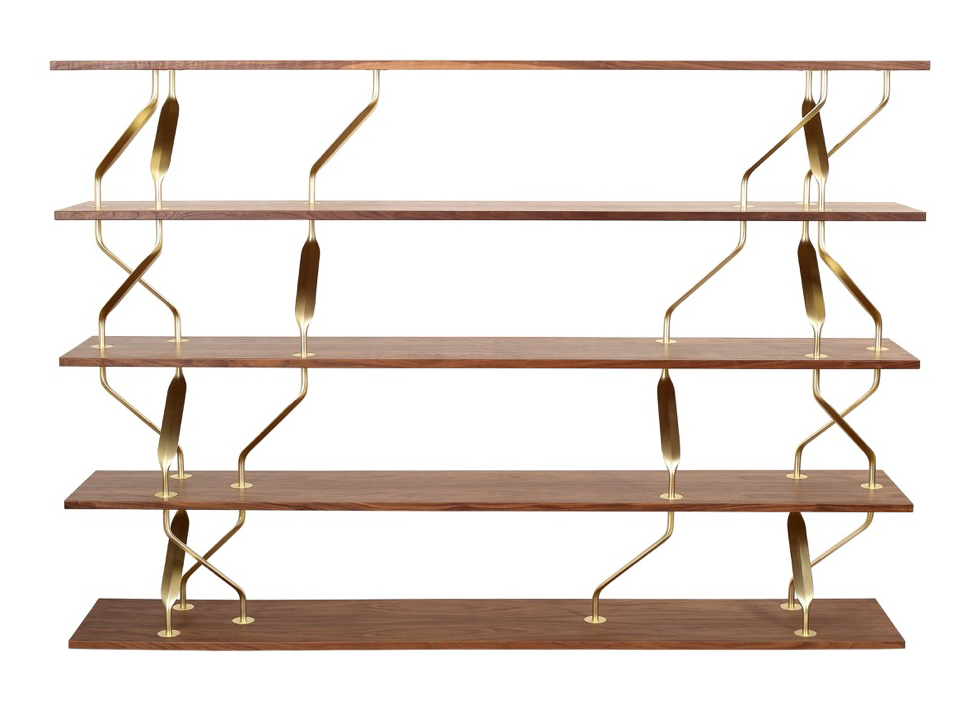
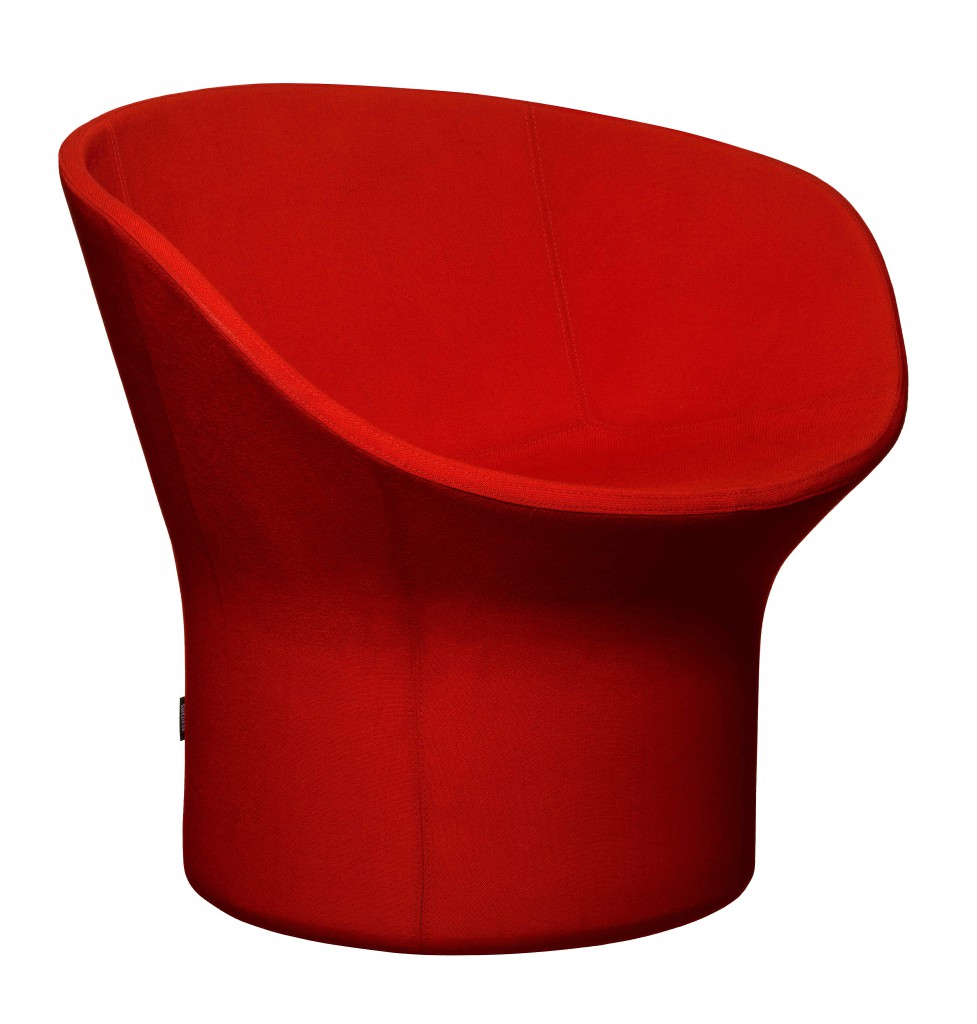
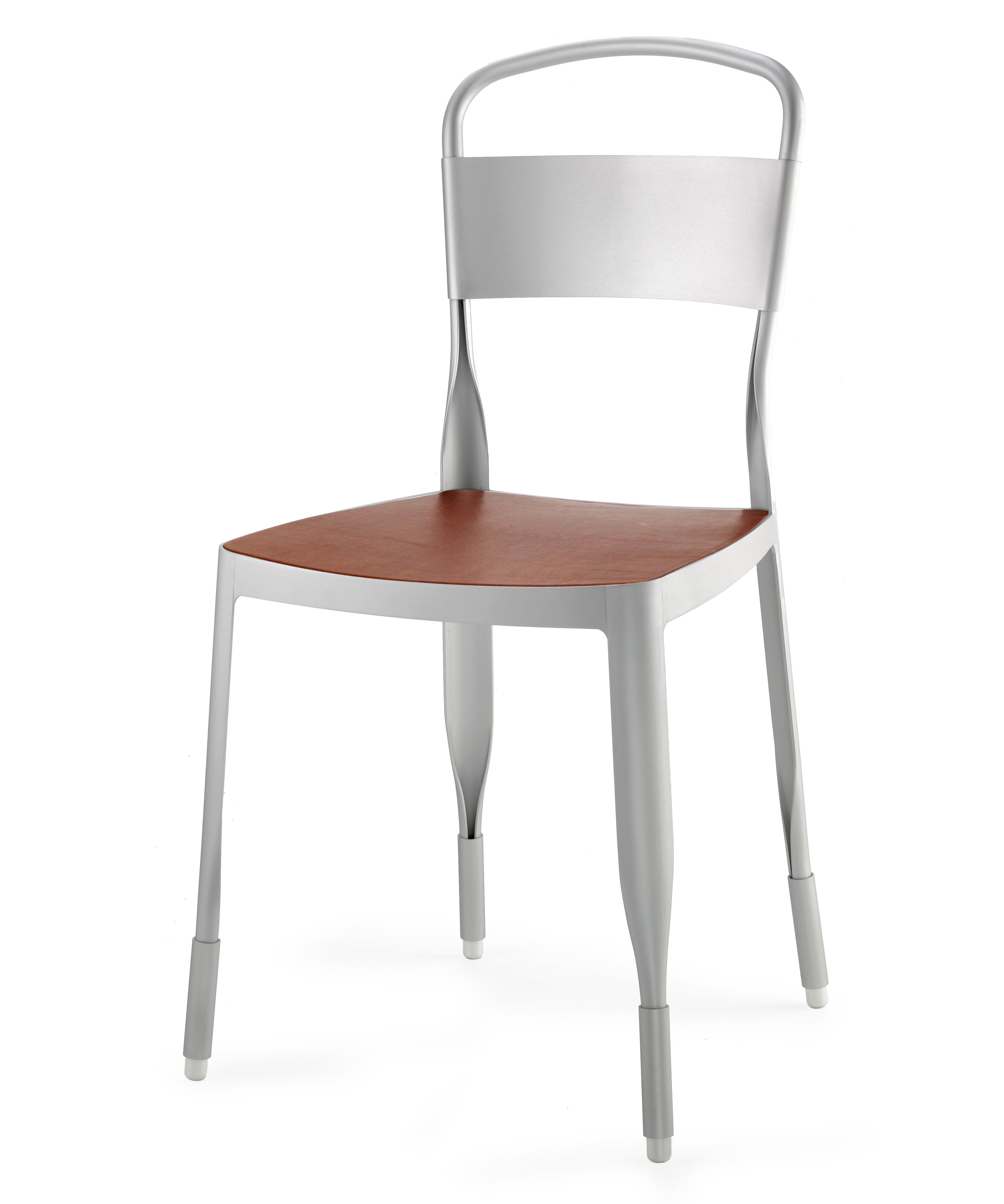