Recasting Craft and Industry: Miguel Giner Gutierrez
We talk to Miguel Giner Gutierrez, winner of the Rado Star Prize at Madrid Design Festival, to discover how he is bringing craft to industrial manufacturing
Young designer Miguel Giner Gutierrez has reimagined how to bring the handmade to industrial casting processes. With his cleverly designed Polymorfo Mold, Gutierrez has designed a way to create bespoke and unique objects with a single mold that can be endlessly adjusted. The mold consists of 3906 beech rods, stacked horizontally into a fixing system which allows Gutierrez to adjust the mold each time it is used to create multiple objects such as cups, bowls, vases and jugs from the single mold.
The first collection produced with the Polymorfo Mold is the Petra Collection. Resembling something between small scale architecture and jagged, weathered cliffs, the ceramic pieces are beautiful in their own right. However, they also serve to demonstrate the potential for applying this way of thinking about industrial-craft manufacturing processed to other cast materials.
Having graduated with a degree in Industrial Engineering & Product Design from the School of Engineering of Terrassa last year, Gutierrez makes a debut at Madrid Design Festival, 2019, in the Rado Star Prize exhibition in which he was awarded the Jury Award for the Petra Collection.
TLmag catches up with Miguel Giner Gutierrez to find out more about his Polymorfo mold and practice at large:
TLmag: What was the brief you set yourself in creating the Polymorfo Mold and the Petra collection?
Miguel Giner Gutierrez : This work took off under the objective of proposing a new form of craft created through innovative design thinking. It was more or less was clear how I could achieve this through a system of profiles and I also knew that I wanted to work with ceramics among other materials. In the end, that was the result —innovation in the crafts revolving around the use of a system of profiles and the infinity of possibilities and combinations that this approach allows.
The polymorfo mold uses design to innovate in the field craftsmanship. With the Petra crockery, I aimed to show the versatility of the polymorfo mold—I wanted to demonstrate how I could create a family of objects of different sizes and shapes, with different functions under this new production process.
So your work sits somewhere between craft production and mass production?
An aspect that I love about the pieces is that they are produced without editions. This is very important to the projects as it is what makes them attractive in that it tells the story of how the pieces have been made. It is a way to see what is behind the works and I hope it raises doubts or questions about the relationship of craft/design/mass production. The project aligns with small-scale production more than mass production with about 60-80 pieces produced in an edition.
What inspired the distinctive aesthetics of the pieces?
Through the mold, I intended to convey the relationship between the ceramic material and nature. The outcome is a purely organic texture that was ruled by the bounded arbitrariness of the tool. It is reminiscent of mineral strata in mountains, rocks eroded by the sea and wind, salt mines and other natural phenomena. In this way, I intend to transport the user to the mineral origin of the material and give value to the product.
Could you explain the design process of developing the mold, I imagine that there must have been a lot of experimentation and trial and error?
The truth is that at first, before the mold, I had to innovate in ceramics for a very practical subject as I had the problem that I did not have much experience with the material which made it difficult to experiment. At first, the material that dominated me.
I entered the world of plaster molds and casting techniques and made molds of virtually any existing vegetable or fruit, always looking for a useful insight, but this was exasperatingly hard to find. In the end, and thanks to the perspective that I had acquired making so many molds, I could see in a mold I made from spaghetti something very interesting.
Then, when I started to develop the Polymorfo mold there was a lot of trial and error and, again, many experiments. It was pure design
thinking, iteration and analysis; making plaster molds in the tool, the use of all kinds silicones, testing different profiles and different sizes, shapes, textures, materials and densities. I made several prototypes exploring thermoforming with the machine in vertical, horizontal and diagonal as well as many theoretical tests. With unlimited budget and time, I think I could have spent my whole life doing tests, prototypes and pieces and still have ideas and projects to do.
In the end, I managed to find a way to dominate the material, to create purely organic forms. The truth is that it has been a pleasure, I enjoyed this project very much.
The Polymorph mold has allowed you to create pieces in ceramic and silicone so far, will you be experimenting with other cast materials in the future?
The logic of creating forms through a profile system is a new idea that has not yet been explored and presents countless possibilities. I have several bullets in the chamber and I am always thinking of things. For example, you could develop a tool for the blown glass technique with the pieces being produced directly in the mold, shortening the number of steps in relation to the traditional technique.
You have just completed your studies in Industrial design, what do you plan to do now?
Right now, I am working in a company with a more technical direction in engineering. What I want is to continue developing, grow as a designer, be creative, create projects related to the simple and everyday aspects of life, with concept and with soul. I want to make useful objects. My dream would be to create my own projects or develop collaborative projects with other disciplines in which my point of view as a designer combined with different disciplinary approaches could add a different scope add and convert the work in something fantastic. I know these goals are not small, but I’m still young and have a long way to develop, I face this challenge with enthusiasm.
This is part of our coverage of the 2019 Madrid Design Festival. To read the rest of the series, click here.
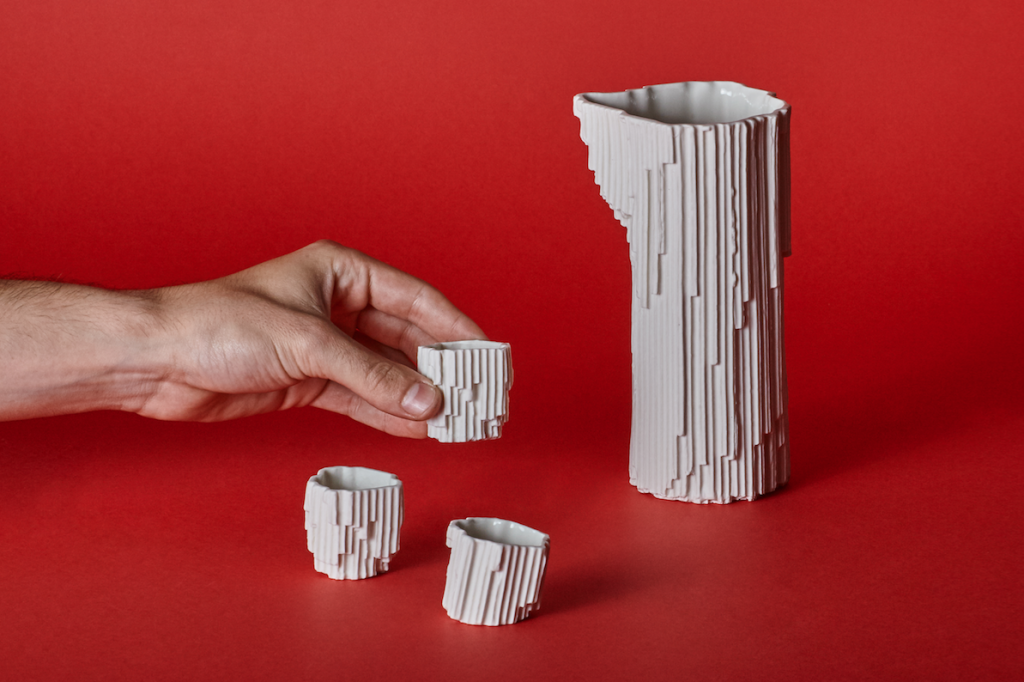

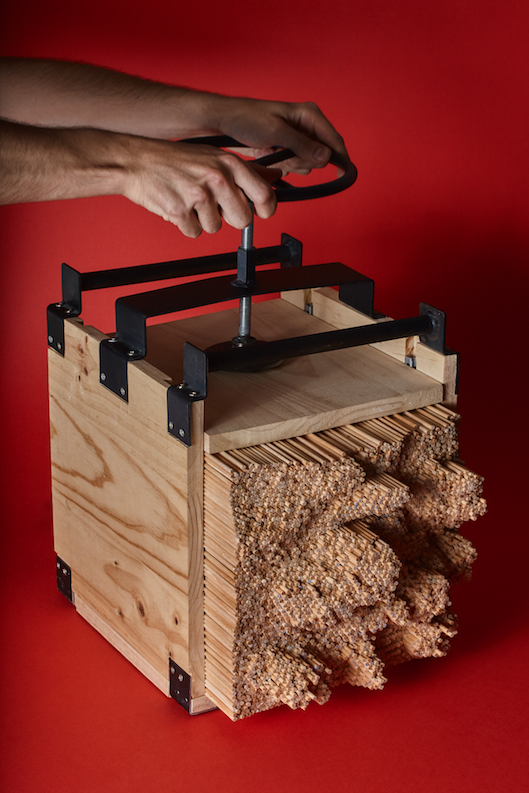
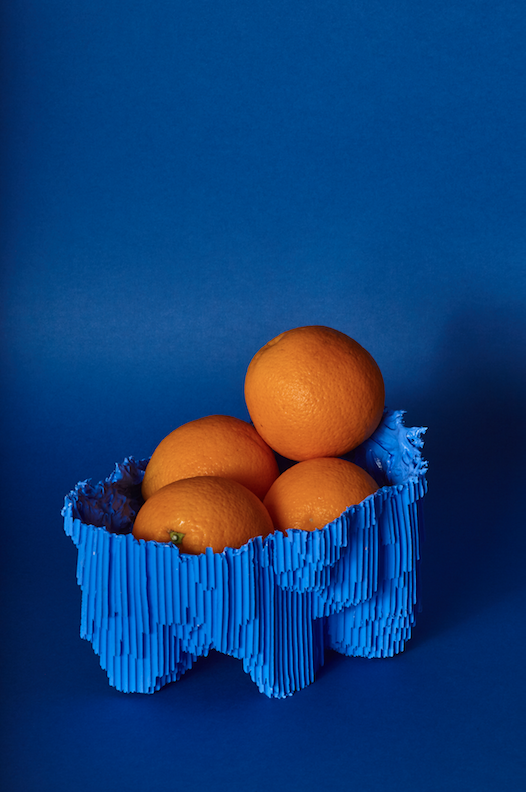
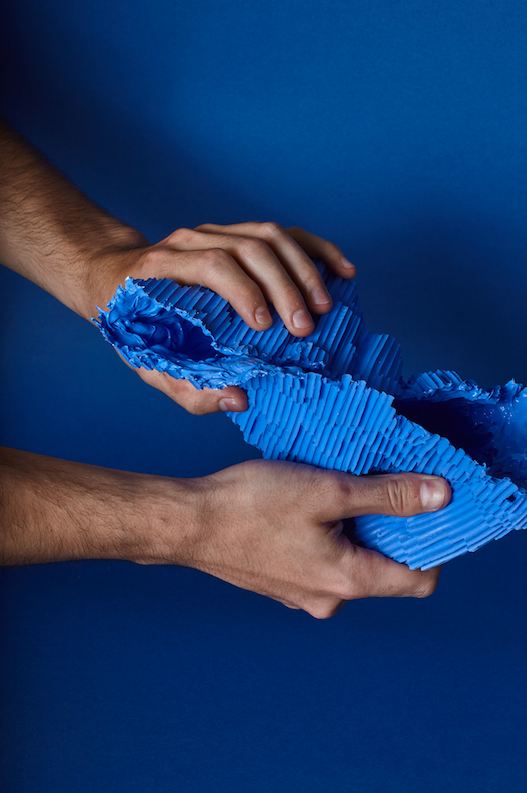
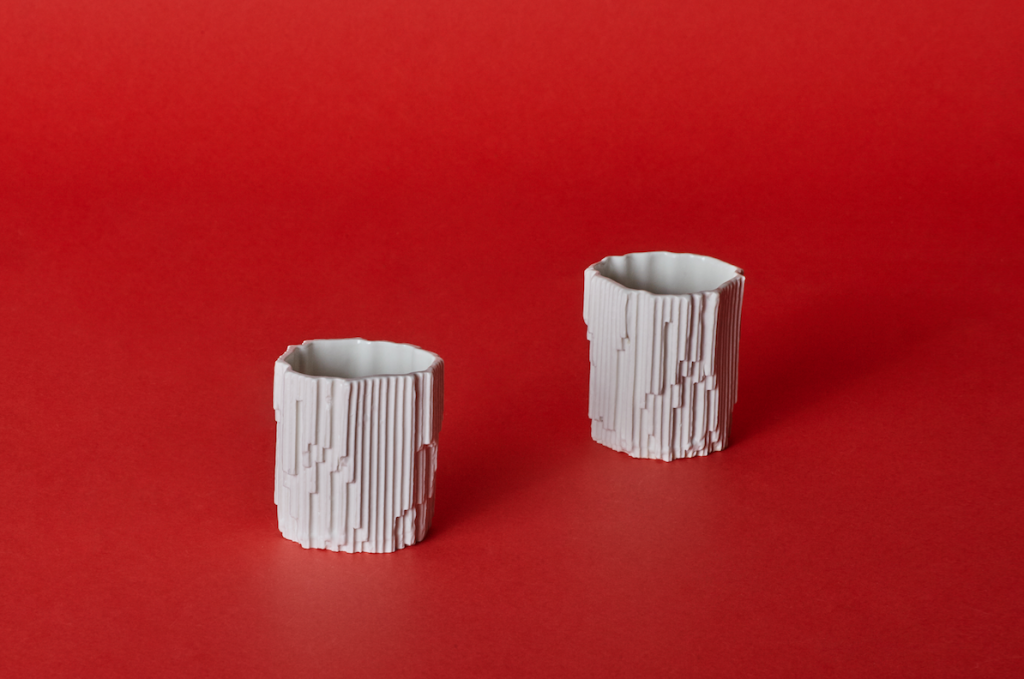
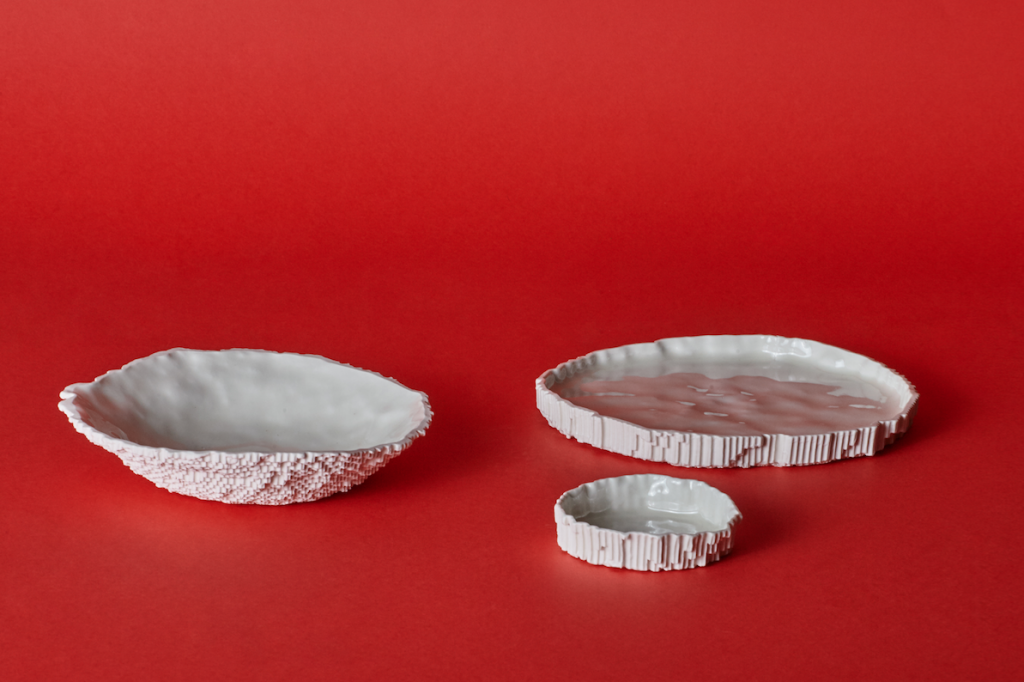