Inflating the Limits of Metal: Oskar Zieta
We catch up with Oskar Zieta about the complexities, challenges and surprises of his iconic inflated metal process and his G-Table series
Architect and designer Oskar Zieta has become synonymous with inflated metal. Seemingly impossible, his industrial balloon-esque works have ranged from architectural scale pieces such as the NAWA sculpture in Wroclaw’s Daliowa Island (2018) to small-scale furniture, perhaps most iconic is his Plopp stool (2008). Since 2000 the designer has been developing and refining the process he developed which involves welding metal and then inflating the structure like a sort of industrial balloon. He calls this process FiDU — or innen druck umformung in German which describes the process of internal pressure forming.
The designer’s company Zieta Prozessdesign revolves around material innovation and craftsmanship and, in 2019 is focusing on color as its recurring theme. However, in trademark style, Zieta is not content simply to add a color finished onto work but instead has developed heat-based processes that chemically change the metal to electric blues and flaming reds amongst other tones.
One of Zieta’s most ambitious projects to date is a series of tables that use the FiDU process paired with the unusual collaborator of algorithms to push the possibilities of inflated metal even further. Entitled G-Tables, the metal legs form a sort of sculpture underneath the variously shaped tabletops.
TLmag catches up with Oskar Zieta to discover the processes and thinking behind each of these bespoke tables:
TLmag: What was the inspiration behind the G-Tables? They seem to be a scaled up, more ambitious version of the Plopp family, was this the starting point?
Oskar Zieta: That’s correct in a way. The starting point where it all began was Plopp stool. Years of experiments and development allowed us to take the designing process to the next level. We created a controllable “construction” customized to user needs, that is a manifesto of “mass customization” ideology. Our clients, who are educated and aware of their needs, seek refined, tailor-made solutions for their interiors.
To create the G-tables, you use a “parametric design algorithm”. Could you explain what this is and why you decided to use it for this project?
The algorithms we use are programs designed specifically to support us in what originally had to be calculated manually or prototyped by hand. It allows us to develop the optimal form, taking into account all the features important to the client, including durability and stability of the structure, the distribution of forces and shape, while allowing us to change the functional and artistic design at every stage. It uses the full potential of modern technologies that surround us every day and takes the designing process to a new level. They allow you to fulfill an artistic vision without worrying about the production and construction aspects.
What are the challenges of creating a G-Table?
Dialogue. The creation of every table is based on a dialogue with a client, as it is made bespoke. The hardest part is to truly understand customer’s needs and work out the perfect solution that is both functional and effective. Sometimes it happens that customers have more vivid imaginations and more crazy ideas than us!
Were there any surprises in the process of creating the G-Tables?
The biggest surprise was the help brought by algorithms. Based on initial parameters, they generate so many optimal solutions, that sometimes it’s difficult to choose the “perfect” one. This motivated us to develop more advanced software that will help us with this task.
Could you explain your thinking behind the materials choices which include different metals such as gold and aluminum for the legs to various woods for the tabletops such as Kauri wood? How do you decide which materials to use and how to combine and pair them?
Our creation process is based on the properties of materials. That is why we select noble metals that provide huge possibilities. Their rawness and beauty are a quintessence of industrial style. Of course, we also test other alloys, both traditional and contemporary, with increased strength. What is more, their plasticity and elegance prove them to be the best choice.
We do our best to enhance their nature by processing them in various ways, to give them exceptional character. Thermal coloring is a good example here, it is a rarely used technology mastered and developed by our company. Heating the objects up and the use of high temperature allows us to achieve the desired color and bring out the surprising beauty of metal without the use of chemical dyes or paints. That’s how we achieve colors like cosmic blue or flamed gold.
Furthermore, we seek unobvious compositions that underline the strengths of the materials by creating symbiosis and determining their power of expression. That’s why we finish our projects with features like Kauri wood, Bog Oak, exotic types of granite or carbon fiber.
You are nominated for the EU mies award 2019, could you tell us about this and what other projects you have in the pipeline for 2019?
It’s a great honor for me as an architect by education. We went through kind of a “loop” from architecture, through design and engineering, to return to architecture again. Creating artistic objects gave us experience and knowledge to use FiDU technology in architectural constructions, such as NAWA nominated to Mies van der Rohe award. What’s more, we are in the stage where, thanks to parametric design, we are able to scale objects such as G-table into a fully functional pavilion. We return to creating art in public space.
Currently, we have several large research projects going on in the field of ultralight constructions and solutions for both industry and architecture.
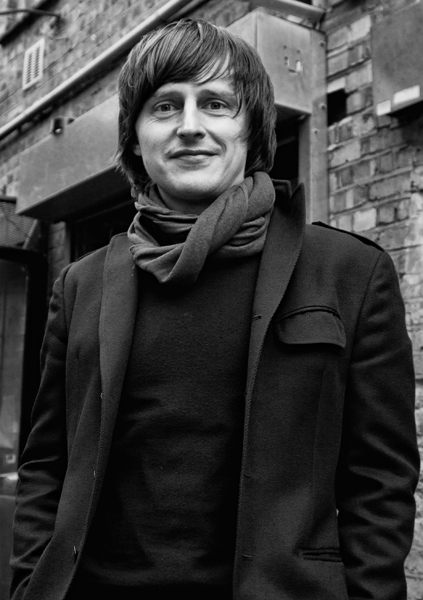
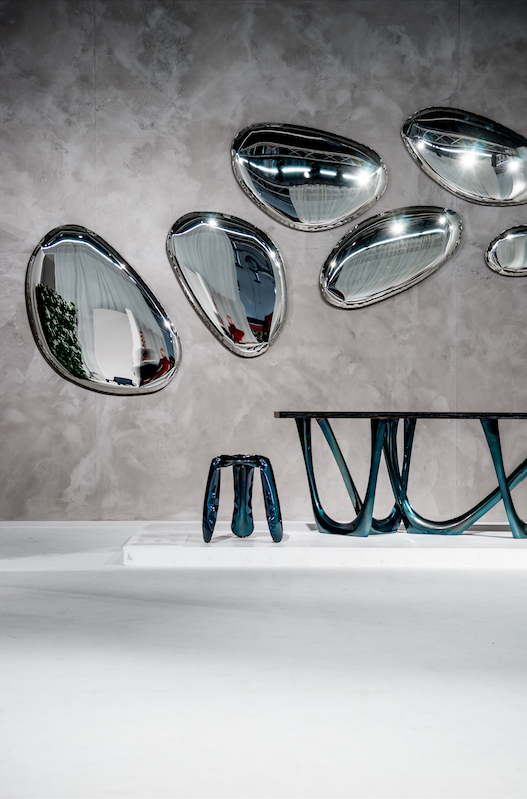

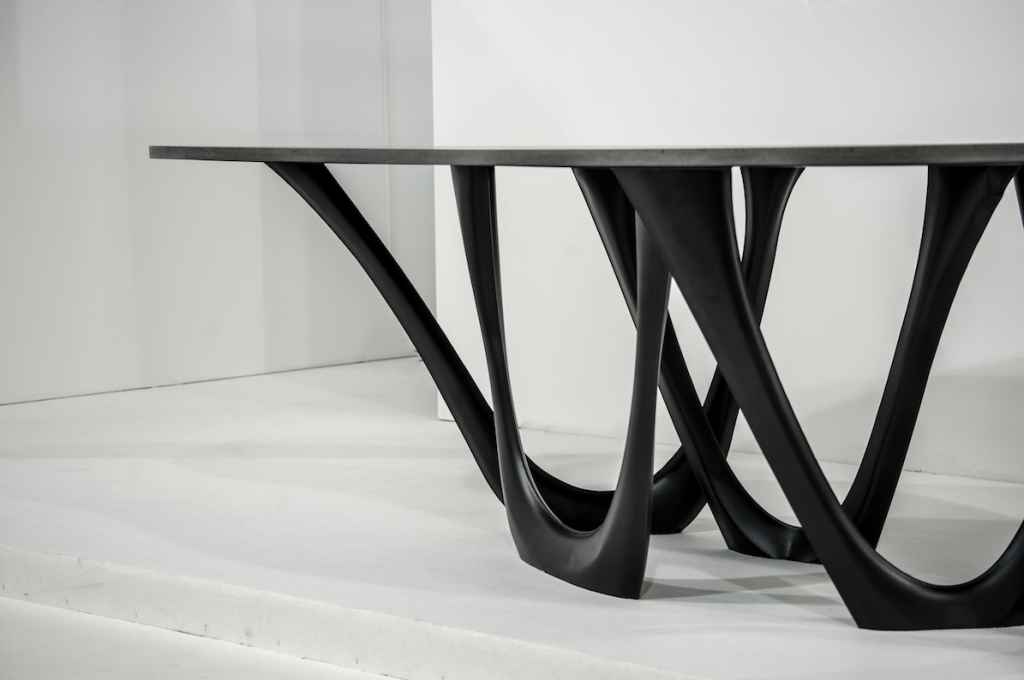
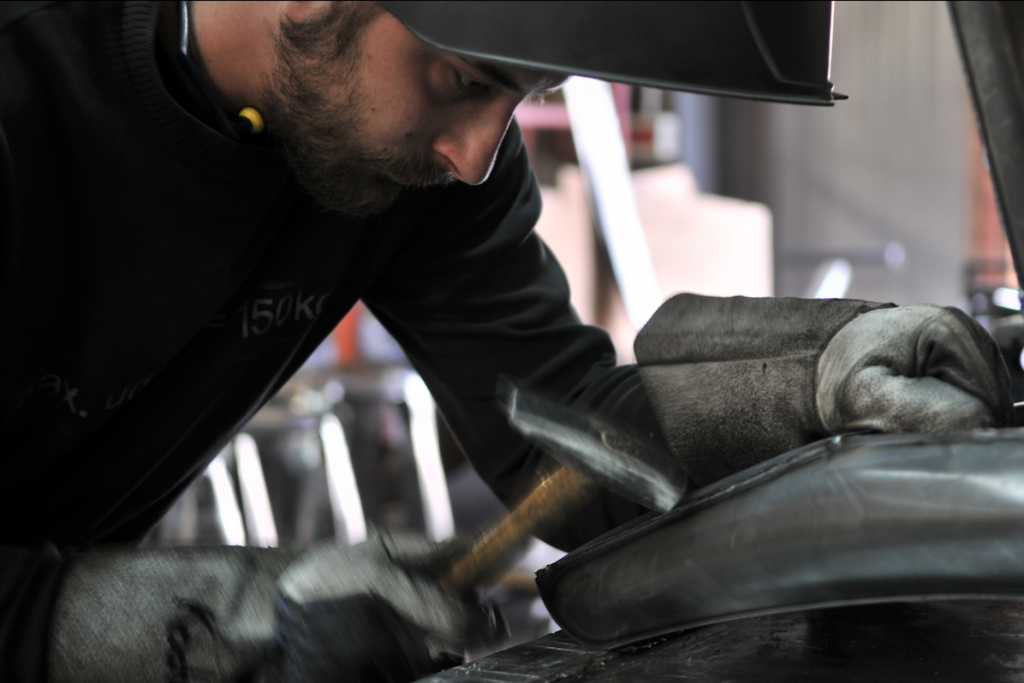